requests then flow to ASD/SSC or to the designated
point in the supply system.
NAMP POLICIES AND PROCEDURES
To be successful in maintenance and material
management, you must follow the policies and
procedures outlined in the NAMP. The following
paragraphs describe some of the NAMP policies and
procedures.
COMMON GOAL OF SUPPLY
AND MAINTENANCE
The common goal of supply and maintenance
organizations is to provide maximum weapons systems
operational readiness. A close liaison between supply
and maintenance personnel is essential in achieving this
goal. It is important that supply and maintenance
personnel have a single point of contact for coordinating
those functions common to both.
MEETINGS BETWEEN SUPPLY AND
MAINTENANCE PERSONNEL
Meetings are held at least weekly between supply
and maintenance representatives. The status of high
priority requisitions is the general topic of the meetings.
These requisitions are the Not Mission Capable Supply
(NMCS), partial Mission Capable Supply (PMCS), and
other related requisitions. Monthly meetings are also
held to resolve problems, establish local procedures, and
promote material support effectiveness.
SPECIAL MATERIAL MANAGEMENT
PROGRAMS
The special material management programs control
critical and costly repairable material used in support of
aircraft maintenance. They are listed as follows:
The Operational Support Inventory (OSI)/Fixed
Allowances Program
The Intensive Repairable Item Management
(IRIM) Program
The Aviation Depot Level Repairable (AVDLR)
Program
The Advanced Traceability and Control (ATAC)
Retrograde Depot Level Repairable (DLR)
Program
Weapons systems are supported under the
OSI/fixed allowance concept. Activities cannot exceed
a negotiated firm allowance without authorization from
the inventory control point (ICP). All assets are carried
on the supply officers record in Purpose code W or L.
Refer to NAVSUPINST 4440.160, FASOINST
4440.15, and FASOINST 4440-16 for additional
information. The supply and maintenance activities
must maintain the one-for-one exchange discipline for
issues of AVDLR items. Pass requisitions off-station
only after the Beyond Capable Maintenance (BCM)
action. However, you may pass requisitions off-station
for anticipated NMCS or items listed in the CRIPL
before processing a turn-in.
The IRIM program, at Navy ICP, standardized
previous programs for intensive management of high
cost and critical repairable items. For aviation
repairable, IRIM replaces the Intensive Closed Loop
Aeronautical Management Program (I-CLAMP). The
objectives of IRIM are to resolve troubled items,
improve turn-around-time (TAT) and carcass returns,
and reduce backorders. Refer to NAVSUPINST 4419.4
and ASOINST 4440.99 for additional information.
The Defense Business Operating Fund (DBOF),
formerly Navy Stock Fund, finances the AVDLR.
Essentially, the DBOF is a revolving accounts of finds
and material. Aviation units pay for DBOF items with
aviation fleet maintenance (AFM) operating finds. In
turn, DBOF uses the payment to replenish the items by
paying for the repair or buying new replacement items.
The benefits of the AVDLR program are reduced
backorders, improved financial flexibility, and
improved aircraft readiness. Also, it is an incentive for
maintenance personnel to effect all repair permitted
under the NAVAIR Aircraft Maintenance Plan.
The objective for establishing the ATAC Retrograde
DLR Program is to improve control of turned in
repairable items. The DLR Carcass Tracking Program
provided improved accountability, traceability, and
customer billing accuracy. Prior to implementation of
ATAC the Program, each activity shipped retrograde to
different repair/overhaul points. Under ATAC
procedures, activities send retrograde to the ATAC hub.
The hubs serve as centralized DLR processing facilities.
Refer to NAVSUPINST 4421.20 for complete ATAC
procedures.
MATERIAL REPORTING
Material reporting is a procedure that uses supply
action documents in support of maintenance. The
9-2
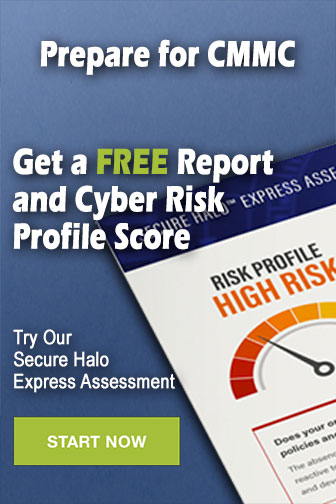