machining, or a combination of these with the action
of solvents or solvent vapors.
Crazing can be caused by improper cleaning,
improper installation, improper machining, or cold
forming. Once a part has been crazed, neither the
optical nor the mechanical defect can be removed
permanently; therefore, prevention of crazing is very
important.
Cleaning Plastic Surfaces
Masking paper should be left on the plastic as
long as possible. When it is necessary to remove the
masking paper from the plastic during fabrication or
installation, the surface should be remasked as soon
as possible. Either replace the original paper or apply
masking tape.
If the masking paper adhesive
deteriorates, making removal of paper difficult,
moisten the paper with aliphatic naphtha, Federal
Specification TT-N-95, type II. Plastic so treated
should be washed immediately with clear water.
For exterior surfaces, flush with plenty of water,
and use your bare hand to gently feel and dislodge any
dirt, sand, or mud. Then, wash the plastic with a
wetting agent, Specification MIL-D-16791, and clean
water.
NOTE: Water containing dirt and abrasive
materials may scratch the plastic surface.
A clean, soft cloth, sponge, or chamois may be
used to apply the soap and water to the plastic. The
cloth, sponge, or chamois should not be used for
scrubbing; use the hand method as described for
removing dirt or other foreign particles.
Dry with a clean, damp chamois, a soft, clean
cloth, or a soft tissue by blotting the surface until dry.
Rubbing the surface of the plastic will induce (build
up) an electrostatic charge that attracts dust particles
to the surface. If the surface does become charged,
patting or gently blotting with a damp, clean cloth will
remove this charge as well as the dust.
To clean interior plastic surfaces, dust the surface
lightly with a soft cloth. Do not wipe the surface with
a dry cloth. Next, wipe carefully with a soft, damp
cloth or sponge. Keep the cloth or sponge free from
grit by rinsing it frequently in clean water.
Cleaning and polishing compound, Specification
P-P-560, may be used to remove grease and oil.
Apply the compound with a soft cloth, rub in a
circular motion until clean,
soft cloth.
Removing Scratches From
You may be required
and polish with another
Plastic Surfaces
to remove and install
canopies, escape hatches, and other aircraft structures
that contain plastic sections. The finish of the plastic
must be protected. Plastic is very soft as compared to
other aircraft structural materials. The surface is
easily scratched or damaged, and should be protected
by the use of proper protective covers and storage
racks, which are provided by the aircraft
manufacturer or manufactured locally. It is easier to
avoid scratches than to remove them. It is possible,
however, to restore even a badly scratched surface to
a good finish by buffing and sometimes sanding.
Aircraft MIMs and SRMs specify limits on the
length, width, and depth of cracks, and in what areas
they are allowed. These measurements are normally
made by the use of an optical micrometer. If a scratch
exceeds the specified limitations, the surface must be
replaced.
Before you sand or buff, be sure the plastic
surface is clean. The buffing wheels and compounds
should also be free of dirt and grit to avoid seriously
scratching the surface during the polishing operation.
If the buffing wheels have been used before, remove
any hardened tallow by running the wheels against a
metal edge.
It is important to remember that most plastic
enclosures are thermoplastic and soften when heated.
The friction of sanding or buffing too long or too
vigorously in one spot can generate enough heat to
soften or burn the surface. Also, plastic that has been
deep-drawn, or formed to compound curvatures, has a
tendency to return to its original thickness when
excessive heat is applied. The best procedure is to
keep either the wheel or plastic constantly in motion
relative to one another. Keep the pressure against the
wheel to a minimum, and change the direction of
buffing often.
The procedures for removing scratches are as
follows: A single deep scratch or imperfection is
reduced by sanding to a number of small, shallow
scratches. These scratches, in turn, are reduced to a
larger number of still smaller scratches on a buffing
wheel to which a fine abrasive is applied. These
finest scratches are further reduced or filled in with
tallow or wax. A final buffing or polishing brings the
surface to a high gloss. The depth of the scratch will
14-2
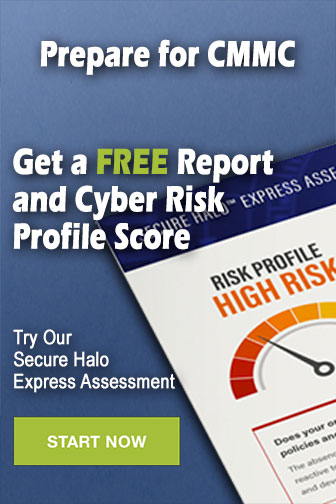