Figure 14-7.Typical loop edge attachment.
method the aircraft manufacturer uses depends upon
the position of the panel in the aircraft, the stresses to
which it will be subjected, and a number of other
factors.
In installing a replacement panel, always
follow the same mounting method used by the
manufacturer of the aircraft.
The following general rules apply to all types of
mountings. Fitting and handling should be done with
masking paper in place, although the edges of the
paper may be peeled back slightly and trimmed off for
installation.
Since transparent plastic is brittle at low tempera-
tures, installation of panels should be done at normal
temperatures. Plastic panels should be mounted
between some type of gasket material to make the
installation waterproof, to reduce vibration, and to
help distribute compressive stresses on the plastic.
Minimum packing thickness is one-sixteenth of an
inch. Rubber, fiber glass impregnate, and nylon are
the most commonly used gasket materials.
Since plastic expands and contracts three times as
much as metal, suitable allowances for dimensional
changes with temperature must be made. Minimum
clearances between the frame and plastic are listed in
Fabrication, Maintenance and Repair of Transparent
Plastics, NAVAIR 01-1A-12, or the applicable MIM.
Clearances should be equally divided on all sides.
Screw torquing procedures should be in
accordance with the applicable MIM. Plastic panels
should not be installed under unnatural stresses. Each
screw must be torqued, as specified in the MIM, to
enable it to carry its portion of the load. If a plastic
panel is installed in a binding or twisted position and
screws are not torqued correctly, the plastic panel may
fail while the aircraft is undergoing normal taxiing
and flight operations.
When you remove a plastic panel, there may be
several different lengths of screws to be removed.
You will save a lot of time by acquiring the habit of
keeping screws separated. An easy way to do this is
to draw a diagram of the panel on cardboard.
Puncture each screw hole, with an awl, through the
cardboard. As each screw is removed from the panel,
it is installed in its respective position on the
cardboard. This is done with each screw as it is
removed.
During installation of the panel, remove each
screw from the cardboard and reinstall it in the same
hole from which it was removed until all of the screws
are reinstalled. If any screws or other fasteners are
damaged during removal or reinstallation, the part
replaced must be the same part number as the
damaged part. Some fasteners are required to be of
nonmagnetic material because of their location near
compasses and other instruments. The specific part
number for each fastener can be found in the IPB for
the aircraft.
REPAIRING REINFORCED PLASTIC
This section deals with the materials and
procedures to be used in repairing reinforced plastic
and sandwich construction components. The
procedures discussed are general in nature. When
actually repairing reinforced plastic and/or sandwich
construction components, refer to the applicable
maintenance instruction manual or structural repair
manual.
The repair of any damaged component made of
reinforced plastic requires the use of identical
materials, whenever they are available, or of
approved substitutes for rebuilding the damaged
portion. Abrupt changes in cross-sectional areas must
be avoided by tapering joints, by making small
patches round or oval instead of rectangular, and by
rounding the corners of all large repairs. Uniformity
of thickness of core and facings is exceedingly
important in the repair of radomes. Repairs of
punctured facings and fractured cores necessitate
removal of all the damaged material, followed by
replacement with the same type of material and in the
same thickness as the original.
All repairs to
14-6
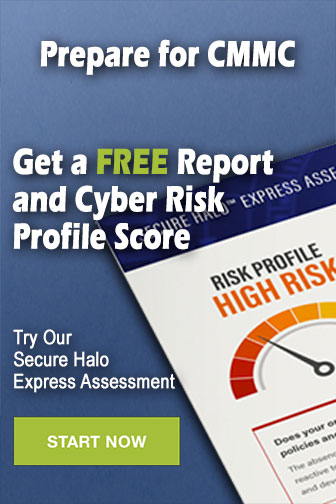