additional analysis, but omit the solvent rinses.
Water, if present, will still appear on the surface of the
filter membrane, but will now tend to spread out
rather than to appear in discrete droplet form.
Examine closely.
NOTE: If 1,1,1-trichloroethane or dry-cleaning
solvent is used as the filtered solvent, the
filter must be dried thoroughly prior to being
placed in petri slide. Either these solvents, or
their fumes, will craze and cloud the
polystyrene petri slides.
Test Filter Analysis
After you process the fluid sample, visually
compare the test filter or patch with the contamination
standards. To determine the particulate contami-
nation level, compare the shade and color of the test
patch with the corresponding colors of the
contamination standards. If the test patch displays a
rust or tan color, use the tan standard patch. If the test
patch is gray, use the gray standard patch. In any
case, you should follow the operating instructions
contained in the contamination standards. Tan
patches occur when rust or iron chlorides are formed
in the system, or the system contains abnormal
amounts of silica (sand). Gray patches are typical of
systems containing normal proportions of common
wear materials and external contaminants.
The maximum acceptable particulate level for
naval aircraft is Navy Standard Class 5. For related
SE, the maximum acceptable particulate level is Navy
Standard Class 3. If visible free water is present in
either the sample bottle or on the surface of the test
filter (at completion of filtration), the system under
test is rejected. A stain on the test filter membrane
may be an indication of the presence of free water.
When a stain is seen on the test filter, obtain a second
fluid sample from the system under test and process it
so that water content can be confirmed prior to system
rejection. Make sure that observed water is not a
result of atmospheric condensation during the
sampling process.
If the system under test fails to meet the Navy
Standard Class 5 particulate requirement or if it
exhibits free water, the system must be decon-
taminated according to the procedures listed in the
applicable MIM.
Filter Bowl Contents Analysis
Hydraulic fluid samples obtained from filter
bowls and/or elements cannot be used to determine
system contamination levels. The following
combination of factors makes the filter bowl sample
useless when determining the systems level of
contamination:
sedimentation, functional location,
and/or an inability to obtain the required
100 milliliters of fluid. Filter bowl residue analysis
may be used to monitor hydraulic system degradation,
monitor for suspected impending component failure,
or isolate a cause for continued contaminant
generation.
Evaluate filter bowl patch residues by following
the procedures in applicable manuals. As you gain
experience about normal contaminates for specific
aircraft systems and hours of operation, you will be
able to evaluate filter bowl patch residue. Through
experience, analysis of main pressure line and case
drain filter bowl residues is useful in verifying failure
of the upstream hydraulic pump, as large amounts of
metal usually show up in these particular assemblies.
Residue in other filter assemblies is affected by so
many other components and factors that analysis is
difficult. Filter bowl residues should be analyzed
only as a means of identifying or verifying suspected
component failure. Examine residue from those filter
assemblies directly downstream from the component.
ELECTRONIC PARTICLE COUNT
ANALYSIS
Electronic particle counters, such as the HIAC
Contamination Test Center, Model C-600-1, or Royco
Electronic Particle Counters, are used to determine
counts of the number of particles in the various size
ranges. The counts obtained are compared with the
maximum allowable under Navy Standard Class 5.
Counts that exceed the maximum allowable in any
size range make the fluid unsuitable for use in Navy
aircraft.
The test results obtained by using automatic
particle counters and the contamination analysis kit
are not always precisely the same.
Both are
authorized for fleet use, and you may use either one.
Automatic particle counters optically sense particles
contained in the fluid sample and electronically size
and count them. Most fleet equipments are calibrated
so that the smallest particle counted has an effective
diameter of 5 microns. Particles smaller than 5
microns, although always present, do not affect the
4-13
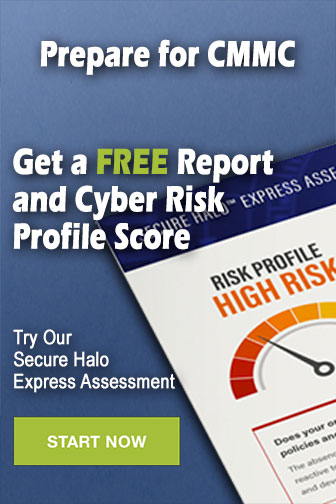