extreme cases, to purge it. Refer to table 4-3. The table
contains information to help you select an appropriate
decontamination method. The table refers to chemical
analysis and particle counting, as well as to the normally
performed patch testing and visual tests. You may request
chemical analysis and actual particle counts of fluid
samples from the NADEP materials engineering
laboratories. You may use these test results to select a
decontamination method.
CONTAMINATION CONTROL SEQUENCE
System decontamination is one operation of a
contamination control sequence that includes
hydraulic fluid sampling and analysis. Decon-
tamination is performed when the results of sampling
and analysis indicate an unacceptable contamination
level. Then, additional testing determines when an
acceptable level is reached.
There are many operations required during the
contamination control sequence, and these operations
interact during the sequence. Figure 4-7 is a basic
contamination control sequence chart for aircraft
system decontamination.
It is a guide for decon-
taminating all naval aircraft and portable hydraulic
test stands. The procedures outlined in the chart
reflect basic requirements of periodic maintenance,
Table 4-3.Aircraft Decontamination Requirements
TEST METHOD
ABNORMAL INDICATION
**DECONTAMINATION
METHOD REQUIRED
Visual Inspection
Free Waterstanding or droplets
Flush
Dissolved Waterpinkish fluid, not clear
Flush
Gelatinous Substances
Flush
Visible Gross Particulate Matter
Flush
Oxidationdark fluid, not clear
Flush
Patch Test
Excessive Particulate-exceeds Class 5
SE Recirculation
Water Droplets or Stains
Flush
Fibers
SE Recirculation
Gross Particulate Matterextreme
Flush
contamination from component failure or
external sources
Particle Count
Excessive Particulate Matterexceeds Class 5
SE Recirculation
Chemical Analysis (Depot)
Viscosityout of limit (*) centistokes @ 100ºF
Flush
Flash Pointless than 180°F
Flush
Waterin excess of(*) ppm
Flush
Neutralizationin excess of 0.8 mg KOH/g
Flush
(acid)
Chlorinated Solventsexceeds (*) ppm
Flush
(*) Acceptable limits to be determined by the cognizant engineering activity.
** Fluid purifiers may be used instead of flushing when purifying equipment is available.
4-18
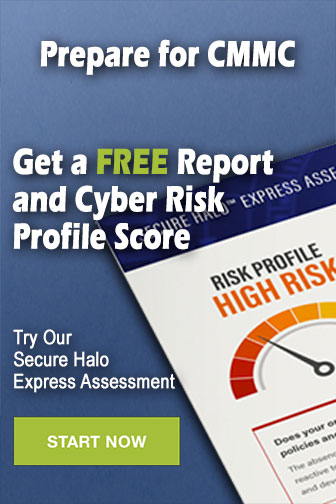