flush, and service the reservoirs or other fluid storage
devices in the contaminated system before system
flushing. If you know that the contamination originated at
an aircraft pump, drain and flush the hoses and lines
directly associated with the pump output. Case drains
should be drained and flushed separately.
If the aircraft filters are suspected of being loaded,
install new or cleaned and tested filter elements in the
aircraft hydraulic filters before flushing. Test stands
must be set up and operated in according to the
requirements of the specific aircraft and the system
being flushed. Adjust the test output pressure and the
flow volume for normal operation of the aircraft system
being flushed.
Monitor the reservoir level in the
portable test stand continuously during the flushing
operation. Use approved fluid-dispensing equipment to
replenish the reservoir before the level decreases to the
half-full point. Depletion of the SE reservoir fluid may
result in cavitation or failure of the test stand pump.
Operate all the circuits (actuators) on the system
undergoing decontamination until the amount of fluid
collected from the aircraft return line is equivalent to
approximately three times the fluid capacity of the
affected system.
Give particular emphasis to the
operation of large displacement actuators, such as those
associated with landing gear and wingfold when
powered by the affected system. Continuously monitor
all the filter differential pressure indicators on the
aircraft and in the SE. Replace any loaded filter
elements. Sample and analyze the system after cycling
of the components.
If contaminant level shows
improvement but is still unacceptable, continue the
flushing operation. If no improvement is observed, try
to find the source of contamination and correct it. If
extensive system flushing fails to decontaminate the
affected system adequately, request assistance from the
cognizant engineering activity.
Upon successful completion of system flushing,
recirculation clean it for a minimum period to
eliminate possible residual debris and to ensure that
the system is in acceptable condition. Sample the
system after recirculation cleaning to verify that
contaminant level is satisfactory. If an unsatisfactory
condition is again indicated, repeat the flushing or
recirculation cleaning operation as required. Upon
successful completion of system decontamination,
service the system to establish proper reservoir fluid
level and to bleed entrapped air.
Purging
Purging is a decontamination process in which the
aircraft hydraulic system is drained to the maximum
extent practicable and the removed fluid discarded.
Then, a suitable cleaning agent is introduced into the
hydraulic system and circulated as effectively as
possible to dislodge or dissolve contaminating sub-
stances. The cleaning operation is followed by
complete removal of the cleaning agent, and then
replace it with new hydraulic fluid. After purging the
system, flushing and recirculation cleaning is
performed to ensure adequate decontamination.
Purging aircraft hydraulic systems is performed only
upon recommendation from, and under the direct
supervision of, the cognizant engineering activity.
The cognizant engineering activity is responsible for
selecting the required cleaning agents, providing
detailed cleaning procedures, and performing tests
upon completion of purging to ensure satisfactory
removal of all cleaning agents. Whenever possible,
purging operations should be accomplished at a naval
aviation depot (NADEP).
NOTE: Organizational and intermediate
maintenance activities are not authorized to
perform system purging.
Purifying
purification is the process of removing air, water,
solid particles, and chlorinated solvents (MIL-C-81302
and MIL-T-81533) from hydraulic fluids. Con-
taminated fluid going to the purifer tower is first filtered
by a 25-micron (absolute) filter. The vacuum applied to
the tower removes air, water, and chlorinated solvents
from the contaminated fluid. As fluid comes out of the
tower, it is filtered through a 3-micron (absolute) filter to
remove solid particles. See figure 4-6. This cycle is
repeated until a desired level of cleanliness is attained.
For systems contaminated with air, water, and
chlorinated solvents MIL-C-81302 and MIL-T-81533,
you can use a purifier to clean the aircraft and support
equipment (SE) to reduce the consumption of fluid and
replace the need for flushing.
SELECTION OF METHOD
The type of contamination present in a system
determines the method by which a system is
decontaminated. Normally, recirculation cleaning is the
most effective decontamination method, considering
maintenance man-hours and material requirements.
This method should be used whenever possible.
However, if a system is contaminated by some
substance other than readily filterable particles, it may
be necessary to flush the system, or in certain very
4-17
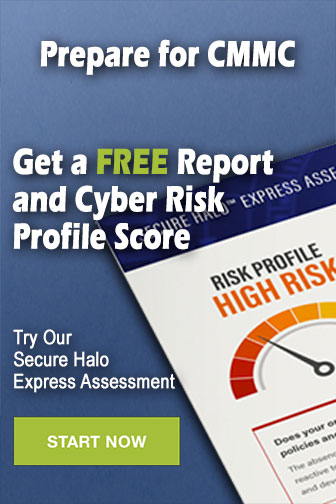