particle count. The contamination analysis kit uses a
patch-test method in which the fluid is filtered
through a test-filter membrane. The sample causes
the membrane to discolor proportionally to the
particulate level. The test filters used have a filtration
rating of 5 microns (absolute). However, they also
retain a large percentage of those particles less than 5
microns in size.
The contamination standards
provided with the contamination analysis kit are
representative of test indications that result if the fluid
sample has a particle size distribution (number of
particles versus size) typical of that found in the
average naval aircraft. Samples from aircraft systems
having typical particle size distributions will,
therefore, show good correlation if tested using both
particle count and patch test methods.
Some operating hydraulic systems have peculiar
design characteristics, so they produce a particle size
distribution different from that found in typical naval
aircraft. Fluid samples from these systems generally
contain an abnormally large amount of siltlike
particles smaller than 5 microns in size. Experience
has shown that this condition results from inadequate
system filtration or from using hydraulic components
that have abnormally high wear rates. It is this type of
fluid sample that could produce different results when
tested, using both particle-counting and patch-test
methods. The difference is caused by the particle
counter not counting those particles smaller than 5
microns, while many of them are retained by the
patch-test filter membrane, causing it to discolor
proportionately.
When test results conflict, the
equipment tested is considered unacceptable if it fails
either test method. The equipment should then be
subjected to decontamination.
You need to recognize that the differing test
results may indicate system deficiencies and justify a
request for an engineering investigation of the
equipment. Poor correlation between particle counts
and patch tests can result from improper
sample-taking procedures, incorrect particle counter
calibration, or faulty test procedures.
These
possibilities must be carefully investigated if a
correlation problem is encountered.
HALOGEN TESTING
The halogen leak detector (fig. 4-5) is used to test
hydraulic fluid samples for MIL-C-81302A (Freon)
or other chlorinated solvents. The detector is a
battery-powered, self-contained instrument. The
instrument provides an audible indication, varying
from a slow ticking sound to a loud squeal, to indicate
the level of the vapor concentration.
You can determine the acceptability of unknown
hydraulic fluid samples by using the HDL-440 leak
detector. To do this, you compare the vapor level of a
known hydraulic fluid to that of the unknown
hydraulic fluid and determine whether the unknown
sample contains more or less than 200 ppm (parts per
million) of chlorinated solvents.
The calibration
standard used in the HDL-440 is hydraulic fluid
MIL-H-5606 or MIL-H-83282, which contains a
known amount (200 ppm) of MIL-C-81302.
DECONTAMINATION
Learning Objective:
Recognize decontami-
nation methods used on naval aircraft and
identify their purpose.
System decontamination is a maintenance
operation performed when a system contains fluid
that is unacceptable because of contamination. The
fluid may be contaminated with foreign matter or it is
not considered acceptable for service for some other
reason. The purpose of decontamination is to remove
foreign matter from the operating fluid or to remove
the contaminated fluid itself. Before you can
decontaminate an affected system, replace any failed
or known contamination-generating components.
Other components of the system are not to be
disturbed, unless required.
Figure 4-5.HDL-440 halogen leak detector in operation.
4-14
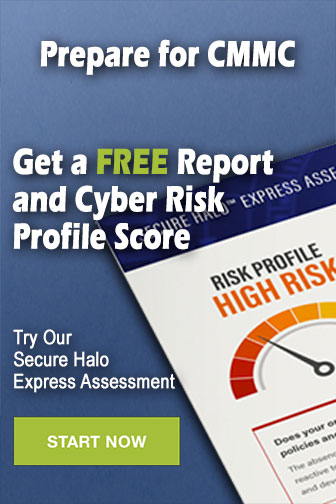