Test stands used for recirculation cleaning must
be equipped with 3-micron (absolute) filtration.
Before connecting the test stand to the aircraft, the
stand itself must be recirculation cleaned and
deaerated, and its contamination level verified to meet
the Navy Standard Class 3 cleanliness level. If the
system has a makeup reservoir, drain and reservice
the system reservoir prior to recirculation cleaning.
Makeup reservoirs have a single fluid port similar to
an accumulator; therefore, little or no fluid exchange
takes place during recirculation cleaning.
If contamination is severe, or if aircraft filters are
suspected of being loaded or damaged, or if
differential pressure indicators have been activated,
install new (or cleaned and tested) filter elements in
the aircraft before you begin cleaning. Set up and
operate the test stand in a manner compatible with the
requirements of the specific aircraft and system being
powered. Adjust the test stand output pressure and
low volume for normal operation of the aircraft
system being recirculation cleaned.
Operate all circuits (actuators) on the system
undergoing decontamination a minimum of 15 complete
cycles, or according to procedures in the specific MIM
or MRCs. Give particular emphasis to the operation of
large displacement actuators, such as those associated
with landing gear and wingfold, when powered by the
affected system.
Continuously monitor all filter
differential pressure indicators, both on the aircraft and
on the portable hydraulic test stand, during the cleaning
process. Replace any loaded fiber elements.
Sample and analyze the system after the cycling
of components.
If the contaminant level shows
improvement but is still unacceptable, repeat the
recirculation cleaning process. If no improvement is
observed, attempt to determine the source of
contamination.
System flushing may be required.
When successful recirculation cleaning is complete,
service the system, as required, to establish the proper
reservoir fluid level and to eliminate entrapped air.
Flushing
Flushing is a decontamination method in which
contaminated system fluid is removed to the
maximum extent practicable and then discarded. It is
a draining process that is generally accomplished by
powering the aircraft system with a portable hydraulic
test stand. See figure 4-6. The contaminated
return-line fluid from the aircraft is then allowed to
flow overboard into a suitable receptacle for disposal.
In effect, filtered fluid from the portable hydraulic test
stand is used to displace contaminated fluid in the
system and to replenish it with clean serviceable fluid.
The amount of fluid removed and replaced during
system flushing varies. It depends upon such factors
as the nature of the contaminant, layout of the system,
and the ability to produce flow in all affected circuits.
Portions of operating systems are often dead ended.
Fluid found in these portions is static and not affected
by the normal system fluid flow. Remove
contaminated fluid in these circuits and associated
components by partially disassembling the unit.
Drain and totally flush the unit.
Generally, system flushing continues until anal ysis
of the return line fluid from the system being
decontaminated indicates that the fluid is acceptable. If
there is severe contamination, considerable quantities of
hydraulic fluid may be expended, making it important to
closely monitor the portable hydraulic test stand
reservoir level, and replenish it as required. Flushing
effectively decontaminates systems containing water,
large amounts of gelatinous-type materials, or fluid that
is chemically unacceptable (containing chlorinated or
other solvents). This type of fluid contamination or
degradation cannot be remedied by conventional
filtration. In severe cases of particulate contami- nation,
such as those that result from major component failure,
flushing techniques may more easily correct the
problem than will recirculation cleaning.
Detailed procedures for flushing hydraulic systems
are found in the aircraft MIMs. The basic procedures
are discussed in the following text, and will give you
some idea of the procedures used when flushing aircraft
hydraulic systems. Remember, use the MIM for the
specific procedures to use when flushing hydraulic
systems. Use flushing to decontaminate systems that
cannot be cleaned by recirculation cleaning or purifying.
Normally, flushing requires you to remove fluids that
are found to be chemically or physically unacceptable,
or fluids contaminated with water, other foreign fluids,
or particulate matter not readily filterable because of its
nature or the quantity involved. Use an external portable
hydraulic test stand to power the contaminate system
and accomplish flushing. Allow return fluid from the
aircraft to flow overboard into a waste container for
disposal. Aircraft subsystems should be operated to
produce maximum displacement of aircraft fluids by
cleaned, filtered fluid from the portable test stand. View
B of figure 4-6 shows fluid flow during system flushing.
Test stands used for system flushing must be
equipped with 3-micron (absolute) filtration and must
have a minimum internal reservoir of 16 gallons. The
stand itself should be recirculation cleaned and
deaerated before it is connected to the aircraft. Drain,
4-16
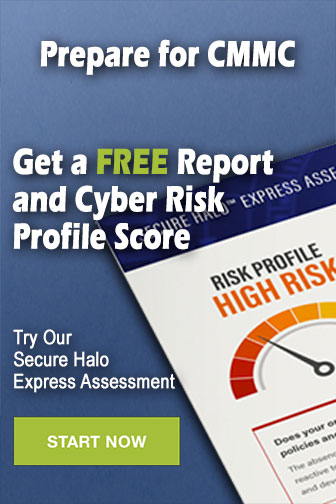