bidirectional or quasi-isotropic. Maximum strength is
parallel to the fibers, and loads at right angles to the
fibers tend to break only the matrix. See figure 14-21.
Metals and composites respond differently when
subjected to loads. See figure 14-22.
The advantages of composites over metals are
higher specific strengths, flexibility in design, ease of
manufacturing, lighter weight materials, ease of
repair (compared to metals), and excellent fatigue and
corrosion resistance. The disadvantages are limited
previous repair information, high start-up costs,
difficulty of inspection, expense of materials, limited
in-work times, poor impact resistance, sensitivity to
chemicals and solvents, environmental attacks, and
the low conductivity of the materials. Advanced
composites are made up of fibers and the matrix.
Fibers are a single homogeneous strand of
material, rolled or formed in one direction, and used
as the principal constituent in composites. They carry
the physical loads and provide most of the strength of
composites. Composite materials are made up of
many thousands of fibers arranged geometrically,
woven or collimated (in columns). The various types
of fibrous materials used today are discussed in the
following paragraphs.
Boron Fibers
Boron was developed in 1959. Boron fibers are
made by using a 0.0005-inch tungsten filament heated
to about 2200°F and drawn through a gaseous mixture
of hydrogen and boron trichloride. A coating of black
boron is deposited over the tungsten filament. The
resulting fiber is about 0.004 inch in diameter, has
excellent compressive strength and stiffness, and is
extremely hard.
Graphite Fibers
High-strength graphite fibers were not developed
until the early 1970s. Fibers of graphite are produced
by graphitizing filaments of rayon or other
polymers in a high-temperature furnace. The fibers
are stretched to a high tension while slowly being
heated through a stabilization process at 475°F in
ambient air. The fibers are carbonized at 2,700°F in
an inert oxygen rich atmosphere, and the
graphitization process takes place at 5,400°F in an
inert atmosphere.
Then the graphite fibers are
subjected to a treatment process that involves cooling
and cleaning of the carbon dust particles to improve
the interlaminar shear properties. These shear
properties relate to the shear strength between
adjacent plies of laminate. The resulting fibers are
black in color and only a few microns in diameter.
They are strong, stiff, and brittle; through control of
the process, graphite of higher tensile strength can be
produced at the cost of lower stiffness. Aircraft parts
are generally produced with fibers of intermediate
strength and stiffness.
Kevlar® Fibers
Kevlar® fibers are a registered trademark of
E. I. DuPont de Nemours & Company Inc, which
maintains exclusive production rights for the fibers.
The structural grade Kevlar® fiber, known as
Kevlar®, is characterized by excellent tensile strength
and toughness but inferior compressive strength
compared to graphite. The stiffness, density, and
cost of Kevlar® are all lower than graphite; hence,
Kevlar® may be found in many secondary structures
replacing fiber glass or as a hybrid with fiber glass.
The fibers are golden yellow in color and measure
.00047 inch in diameter.
Matrix
Although the fibers are the principal load-
carrying material, no structure could be made without
the matrix. The matrix is a homogeneous resin that,
when cured, forms the binder that holds the fibers
together and transfers the load to the fibers.
The most common matrix material in current use
is epoxy. Epoxies provide high mechanical and
fatigue strength; excellent dimensional stability,
corrosion resistance, and interlaminar (between two
or more plies) bond; good electrical properties; and
very low water absorption.
The changing of the
matrix properties (hardening) by a chemical reaction
is called the cure. Curing is the changing of the
matrix properties (hardening) by a chemical reaction.
Curing is usually accomplished with heat and vacuum
pressure.
The finished product may be a single-ply
(lamina) or a multiply product called a laminate.
Laminate
A lamina is a single-ply arrangement of uni-
directional or woven fibers in a matrix. A lamina is
usually referred to as a ply. A laminate is a stack of
lamina, or plies, with various in-plane angular
orientations bonded together to form a structure.
14-20
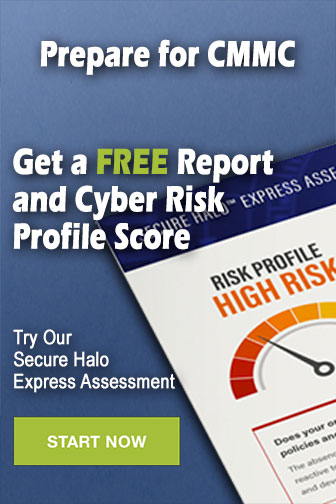