80 percent composites. As a structural mechanic, you
will be required to maintain these new types of
aircraft.
To be proficient, you must be able to
recognize the types of damage, understand the
processes involved in damage assessment, inspection,
and repair of composite materials. As new materials
are introduced, new repair procedures will be
required. It will be your responsibility to keep abreast
of these developments.
Composite materials damage may be categorized
as either environmental or physical. Environmental
damage includes crazing and cracking caused by solar
and ultraviolet radiation, water absorbed through
humidity and rain, and lightning strike damage.
Lightning strikes can cause holes to be burned in the
structure, puncturing and splintering, and it has been
known to weld bearings and hinges. Physical damage
is caused by an applied force or deficiency in
fabrication, such as dents, scratches, cracks, cuts and
abrasions, pits, voids, disbonds, delamination, core
crush on sandwich structures, and impact damage.
ASSESSMENT OF COMPOSITE
MATERIAL DAMAGE
The task of repair begins when you determined
that the structure has been damaged and that the
damage is sufficient to require the structure to be
repaired. The existence of damage may be obvious,
such as a skin penetration, a gouge, or a dent. Con-
versely, the proper identification and classification of
the damage may be difficult. Because of the brittle,
elastic nature of composite laminate materials, for
example, the fibers may break upon impact, but then
spring back, leaving little visible indication of
damage.
There are three distinct steps involved in damage
assessment. The first step is to locate the damage.
The second step is to evaluate the defect to determine
such information as the defect type, depth, and size.
This information is important because the method of
repair will vary, depending on this information. The
third step is to re-evaluate, after defect removal (as
applicable), the area being repaired.
DAMAGE INSPECTION METHODS
There are many methods available for locating
and evaluating the damage. Ideally, the fastest
method that will reliably find the appropriate type and
size of defect should be employed since recurring
costs will probably outweigh nonrecurring equipment
procurement costs. Some of the inspection methods
to be discussed are visual inspection, tap test, X-ray,
and ultrasonic inspection methods.
Visual Inspections
Visual inspections are a methodical search for
defects, checking for obvious damages. Be
suspicious of any nick, dent, or paint chip because
there may be underlying damage. Many types of
defects, such as impact damage, corrosion, and
delamination, cannot be detected by visual
inspections alone.
Tap Testing
A tap test is used in conjunction with a visual
inspection, and is an elementary approach to locating
delaminations, disbonds, core damage, water, or
corrosion.
Tapping should be done with a small
hammer about the weight of a US 50-cent coin. A dull
or dead sound indicates that some delamination or
disbond exists. A clear, sharp sound indicates a solid
structure.
Tap testing is limited to finding defects
close to the surface, and is ineffective in areas of
sharp contours and changes in shape.
X-ray Inspections
X-ray inspections use the same basic process as a
dentist uses to X-ray teeth. The penetrating power of
the radiation is used to reveal the interior of objects
and to record it on film.
Defects in material
essentially change the thickness of the material, thus
changing the degree of absorption of radiation. More
radiation passes through the thinner area of a part, and
shows up as a darkened area on the developed film.
Ultrasonic Inspections
Ultrasonic inspections use sound wave fre-
quencies higher than the human hearing level, above
20,000 Hz, to penetrate the part. It measures the time
the transmitted sound waves take to pass through the
object and return to the receiver. The signals are
changed into a display on a cathode-ray tube that
provides a means of interpreting defects. Accurate
results are dependent on an experienced operator,
clean surface, known standards of part construction,
and repeatability of indications.
14-23
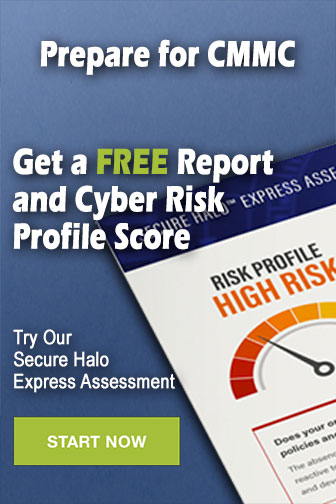