Table 14-1.Aircraft Advanced Composite Application Usage
Composites are attractive structural materials
classified by the composition of the reinforcing
because they provide a high strength-to-weight ratio
and offer design flexibility. The function of a
composite is to replace heavy/dense metals with
stronger, lighter weight structural components,
allowing lightweight aircraft to carry payloads farther
distances using less fuel. In contrast to traditional
materials of construction, these materials can be
adjusted to more efficiently match the requirements of
specific applications.
These materials are highly susceptible to impact
damage, with the extent of damage being visually
difficult to determine. A nondestructive inspection
(NDI) is required to analyze the extent of damage and
effectiveness of repairs.
Composites are classed by the type of reinforcing
elements. These elements may be fibers, particle,
flake, or laminar materials. They are further
materials and by the type of matrix materials.
The primary factors taken into consideration
when designing composites are the costs (research
and development, production, fuel economy), type of
application (load requirements of the structure,
adjoining materials, service-life requirements),
mission and maintenance requirements, and
operational environment (hot/cold weather, relative
humidity, altitude, land/carrier based).
The comparative properties of composites and
metals are that metals have almost the same physical
and mechanical strengths equal in all directions.
Stresses and strains are equally transmitted in all
directions.
Composites can have different physical
and mechanical strengths in different directions, and
are considered to be anisotropic or quasi-isotropic.
These strengths are determined by the fiber
orientation patterns. The patterns are unidirectional,
14-19
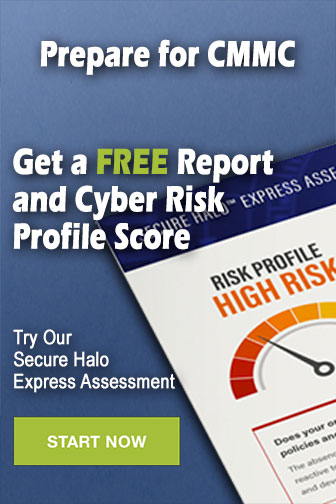