Damage repairsContinued
fatigue, 13-36
foreign object, 13-36
hardness testing, 13-37
heat, 13-37
inspection for cracks, 13-37
investigation of damage, 13-37
stress, 13-37
visual inspection, 13-37
Damage repairable by insertion, 13-38
Damage repairable by patching, 13-38
Damage requiring replacement, 13-38
Damper cylinder, 12-66
Decontamination, 4-14
flushing, 4-16
purging, 4-17
purifying, 4-17
recirculation cleaning, 4-15
Demountable flange wheel, 11-1
Density, 1-23
Density altitude, 10-2
Diagrams, 3-11
Differential pressure indicators, 7-34
Dimple countersinking tools, 13-10
Direct current, 15-8
Direct lift control (DLC), 9-44
Directional control systems, 1-9,9-18
Directional trim, 9-50
Dismounted inspection, 11-18
Dissymmetry of lift, 10-2
Divided (split) wheel, 11-1
Double-acting actuating cylinder, 8-2
Drilling rivet holes, 13-28
Drills, 13-8
Drop check procedures, 12-18
Drying sealants, 14-44
Du Pont Teflon® filled polyurethane paint, 14-34
Dual installations, 11-28
Dual disc brakes, 12-37
Ductility, 1-23
Dye penetrant inspection, 15-13
Dynatube fitting repair, 6-28
Dzus fasteners, 2-8
E
Eddy current inspection, 15-11
coils and probes, 15-12
test coil configurations, 15-12
Elasticity, 1-23
Elastomeric rain erosion-resistant coating
MIL-C-7439, 14-35
Electric solenoid shutoff valve, 7-26
Electrical components, 12-14
Electrical failures, 3-19
Electrical wire and cable, 2-42
bonding, 2-43
connectors, 2-43
terminals, 2-43
Electrically controlled nose steering system, 12-12
Electrically controlled nose steering system mainte-
nance, 12-14
adjustment of components, 12-16
bleeding the system, 12-16
operational check, 12-14
troubleshooting, 12-16
Electrodes, 15-32
Electronic control, 9-45
Electronic control systems, 9-19
Electronic particle count analysis, 4-13
Elevator control system, 9-3
Emergency brake system, 12-35
Emergency flap system, 9-40
Emergency power systems, 7-5
INDEX-5
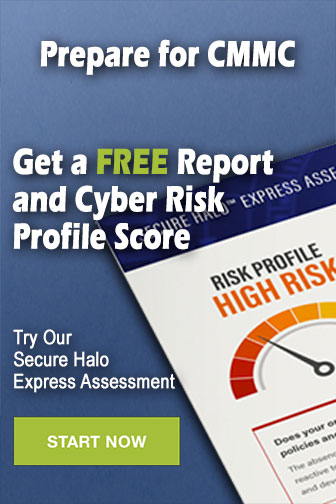