TORQUING COMPUTATION
When you are using a drive-end extension, the
torque wrench reading must be computed using the
following formula:
where:
S = handle setting or reading
T = torque applied at end of adapter
La = length of handle in inches
Ea = length of extension in inches
If you desire to exert 100 inch-pounds at the end of
the wrench and extension, when La equals 12 inches and
Ea equals 6 inches, it is possible to determine the handle
setting by making the following calculation:
S = 66.7 inchpounds
Whenever possible, attach the extension in line with
the torque wrench. When it is necessary to attach the
extension at any angle to the torque wrench, the effective
length of the assembly will be La + Ea, as shown in figure
3-12. In this instance, length Eb must be substituted for
length Ea in the formula.
NOTE: It is not advisable to use a handle
extension on a flexible beam-type torque
wrench at any time. The use of a drive-end
extension on any type of torque wrench makes
use of the formula necessary. When the formula
has been used, force must be applied to the
handle of the torque wrench at the point from
which the measurements were taken. If this is
not done, the torque obtained will be in error.
LUBRICATION
Learning Objective: Recognize different types
of lubricants, methods of application, and use
of lubrication charts.
Perhaps the only connection you have had with
lubrication was taking the car to the garage for greasing
and oil change. If your car ever burned out a bearing,
you have learned the importance of lubricants, The
proper lubrication of high-speed aircraft is very
important. You should be familiar with the various types
of lubricants, their specific use, and the method and
frequency of application.
Lubricants are used to reduce friction, to cool, to
prevent wear, and to protect metallic parts against
corrosion. In the aircraft, lubrication is necessary to
minimize friction between moving parts. Only the
presence of a layer or film of lubricant between metal
surfaces keeps the metals from touching. As a result,
friction is reduced between moving parts. Prolonged
operating life is ensured when the lubricant keeps metal
surfaces from direct contact with each other. If the film
disappears, you end up with burned out or frozen
bearings, scored cylinder walls, leaky packings, and a
host of other troubles. Appropriate use of proper
lubricants minimizes possible damage to equipment.
LUBRICANTS
You can get lubricants in three forms. hey are
fluids, semisolids and solids. Additives improve the
physical properties or performance of a lubricant. We
all know that oils are fluids, and greases are semisolids.
You probably think of graphite, molybdenum disulfide,
talc, and boron nitride as additives. In fact, they are solid
lubricants. A solid lubricants molecular structure is
such that its platelets will readily slide over each other.
Solid lubricants can be suspended in oils and greases.
There are many different types of approved
lubricants in use for naval aircraft. Because the
lubricants used will vary with types of aircraft and
equipment, it is impractical to cover each type. Some of
the more common types are described in table 3-5.
Methods of Application
Different types of lubricants maybe applied by any
one of several methods. Common methods are by grease
gun, by oil/squirt cans, by hand, and by brush.
GREASE GUNS. There are numerous types and
sizes of grease guns available for different equipment
applications. The lever and one-handed lever guns are
two of the most common types in use. The grease gun
may be equipped with a flexible hose instead of a rigid
extension. Different nozzles can be attached to the
3-22
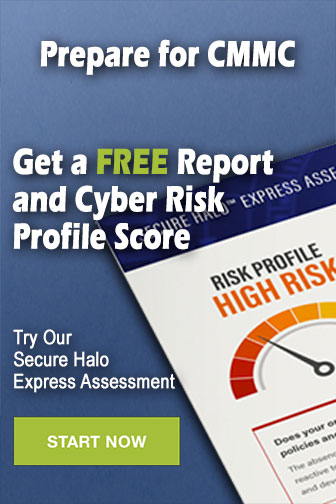