Each trouble analysis procedure provides
preliminary data, such as tools and equipment,
manpower requirements, and material. In the block type
of troubleshooting sheets, the procedure is arranged in
the order of most likely occurrence. The sheet contains
a NO-YES response to direct maintenance personnel
through a logical series of steps. These directed
responses assist in isolating the malfunction. When the
requirements of a step are satisfactory, you go to the
YES column and perform the referenced step. When the
requirements of a step are not satisfactory, you go to the
NO column and perform the referenced step. This
method is continued until the malfunction is isolated and
corrected. The original checkout procedure must then
be repeated to ensure that the malfunction has been
corrected.
TROUBLESHOOTING PROCEDURES
Troubleshooting procedures are similar in
practically all applications, whether they be mechanical,
hydraulic, pneumatic, or electrical. These procedures
are certainly adaptable to all aircraft maintenance, as
well as other types of installations. Auto mechanics use
these steps to find and repair malfunctions in
automobiles. You will use the same procedure to find
and repair malfunctions within aircraft systems.
Clarification of the seven distinct troubleshooting
steps previously mentioned are as follows:
1. Conduct a visual inspection. This inspection
should be thorough and searching-checking all lines,
units, mechanical linkage, and components for evidence
of leaks, looseness, security, material condition, and
proper installation. During this visual inspection, the
hydraulic system should be checked for proper
servicing-reservoir for proper level, accumulators for
specified preload, etc.
2. Conduct an operational check. The mal-
functioning system or subsystem is checked for proper
operation. This is normally accomplished by attaching
the support equipment to the aircraft, which supplies a
source of electrical power and pressurized fluid to
operate the hydraulic system. In some instances,
however, the aircraft may be ground checked by using
aircraft power and equipment. Whatever the case,
during movement of the malfunctioning unit, the AM
checks for external leakage, the correct direction of
component movement, its proper sequence of operation,
speed, and whether the complete cycle was obtained.
3. Classify the trouble. Malfunctions usually fall
into four basic categorieshydraulic, pneumatic,
mechanical, and/or electrical. Using the information
gained from steps 1 and 2, the AM determines under
which classification the malfunction occurs.
Something affecting normal flow of hydraulic fluid
would be classified under the hydraulic classification.
The flow of fluid may be affected by external and
internal leakage, total or partial restriction, or improper
lubrication.
Something affecting the normal flow of compressed
gases is classified as a pneumatic malfunction. This type
of malfunction stems from the same general sources as
hydraulic malfunctions mentioned in the previous
paragraph.
Most units that operate hydraulically or pneumat-
ically incorporate mechanical linkage. If a discrepancy
in the linkage exists, it will affect the systems operation.
Mechanical discrepancies should be found during visual
inspections, and they are usually in one of the following
categories: worn linkages, broken linkages, improperly
adjusted linkages, or improperly installed linkages.
Many hydraulic units incorporate electrical compo-
nents to operate or control them. You must be able to
determine if the electrical system is functioning
normallyelectrical malfunctions will usually be a
complete power failure, circuit failure, or component
failure.
4. Isolate the trouble. This step calls for sound
reasoning, a full and complete knowledge of hydraulic
theory, as well as a complete understanding of the
affected hydraulic system. During this step, you must
use your knowledge and the known facts to determine
where the malfunction exists in the system. Usually the
trouble can be pinned down to one or two areas. This is
done by eliminating those units that could not cause the
known symptoms and those that can be proved to be
operating normally.
5. Locate the trouble. This step is used to eliminate
unnecessary parts removal, thus saving money, valuable
time, and man-hours. Often, you have determined what
unit or units in the system could have caused the
malfunction, thus verifying the isolation step.
Both hydraulic and pneumatic malfunctions are
verified in the same manner. You remove lines and
inspect them for the correct flow in or at the suspected
unit. Internal leaks may occur in valves, actuators, or
other hydraulic units. Any unit that has a line that could
carry fluid to return is capable of internal leakage.
Mechanical malfunctions are located by closely
observing the suspected unit to see if it is operating in
3-17
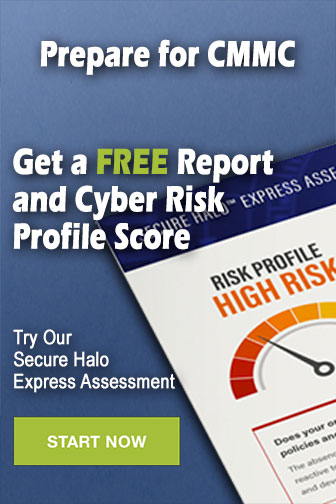