O-LEVEL MATERIAL CONTROL
CENTERS
While performing maintenance on a squadron
aircraft, you find that you must remove a
malfunctioning part. The maintenance chief agrees;
so, you wrap the unserviceable item in the approved
wrapping material or put it in the proper container.
You complete all the required information, ensuring
accuracy, in NALCOMIS or fill out the VIDS/MAF,
making sure that the entries are readable on all five
copies. Then, you take the VIDS/MAF to the squadron
material control center.
The material control center is your squadrons
contact point for parts and material. The material
control center passes the requirements to the
ASD/SSC of the supply department. The material
control center does this in a timely manner to prevent
work stoppage. When the parts arrive, your squadron
AK ensures that the replacement parts are forwarded
to your work center after receipt from supply.
AKs in the material control center perform other
duties in addition to filling material requirements. The
material control center prepares documents for
material required for operational support: for example,
indirect material requirements, such as aviation fuel
and lube oil, that the squadron uses in the aircraft. The
material control center also provides flight clothing
and special equipment (such as safety shoes and foul
weather jackets). Also, squadron AKs make up
requests for material carried in the service market
(SERVMART) outlets. Often, they are the gopher
on SERVMART runs. Squadron AKs ensure that
personnel prepare surveys for lost, damaged, or stolen
material. They keep maintenance control advised of
the overall supply situation and its effect upon the
maintenance actions. The material control center also
performs accounting and charting of operational target
(OPTAR) funding and budgeting. Material control
also validates NMCS and PMCS requisitions to make
sure that supply is carrying all the outstanding
requisitions on their list. Finally, the AK is the
individual your supervisor will contact when he or she
submits an IMRL change request.
The material control center also prepares and
accounts for flight packets. While assigned to a
squadron, you may be deployed away from your home
base. If aircraft parts fail or if you need to buy gas or
oil while deployed, the flight packet prepared by your
squadron AK will contain the paperwork to pay for the
services you receive, whether the activity that provides
the parts or services is a Navy activity or some other
activity. A flight packet has the following items.
DOD Single Line Item Requisition System, DD
Form 1348 (6 part). This DD Form 1348 allows a
military activity rendering a service to bill your
squadron. The pilot of the aircraft enters what was
purchased, the number purchased, and the date. He or
she signs the requisition as proof of receipt.
Purchase Order Invoice Voucher, Standard Form
44. Commercial as well as government activities accept
these vouchers in payment for goods and services. There
are monetary limits placed on the Standard Form 44s,
and if the pilot wishes to exceed this limit, he or she must
get permission from his or her commanding officer. The
flight packet contains instructions on how to fill out
these forms. Because Standard Form 44s can have
monetary value, the pilot accounts for each voucher in
his or her possession.
DD 1896 or DD 1897 (identiplate). This
identiplate is used to procure jet fuel or aviation gasoline
from commercial airports holding Defense Logistics
Agency, (DLA) into-plane refueling contracts and most
DOD activities.
I-LEVEL MATERIAL
CONTROL CENTER
The material control center at the I-level operates
like the material control center in a squadron. The
difference is in the volume of the parts requisitioned.
The volume can be two or three times greater at the
I-level than at the O-level. The volume is greater
because the I-level maintenance activities repair more
than 90 percent of the unserviceable parts turned in by
the squadrons.
The aeronautical material screening unit (AMSU)
processes components turned in to the ASD/SSC
(aviation support division/supply support center) to
determine the capability of the intermediate
maintenance activity (IMA) to check/test or repair the
item. The AMSU makes this determination by using
the ICRL. The supply managers at the IMA consult
maintenance personnel about ICRL management.
They also support local efforts to improve repair
capability.
Q22. What work center is the point-of-contact for
parts and material at the organizational
maintenance level?
3-22
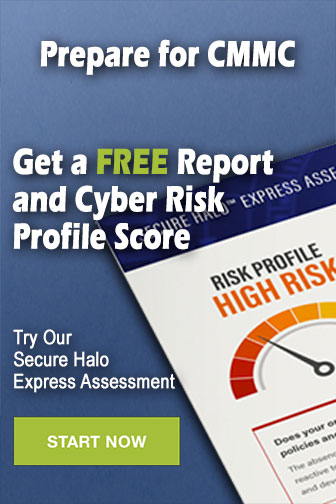