CHAPTER 4
CORROSION PREVENTION AND CONTROL
As a maintenance crew member, you will work in
two main areas when combating corrosion on naval
aircraft. These areas include aircraft structures and
avionics corrosion control.
AIRCRAFT STRUCTURES AND
CORROSION
LEARNING OBJECTIVES: Describe how
metal corrosion can threaten the structural
integrity of an aircraft. Identify the personnel
required to obtain corrosion control training.
Identify the primary reason for selecting
materials in aircraft construction.
Modern high-speed aircraft depend on the
structural soundness of the metals that make up the
largest percentage of their thousands of parts. Metal
corrosion is the greatest threat to the soundness of
metals and to the structural integrity of an aircraft. The
materials used to construct an aircraft are designed to
carry certain loads, to withstand given stresses, and to
provide strength for safety. Corrosion reduces the
strength and changes the mechanical characteristics of
the materials, thus endangering the aircraft and
reducing the margin of safety.
The corrosion that occurs on avionics equipment
is similar to that which occurs on the basic airframe
structure. The main difference is the amount of
corrosion that is detrimental. A small amount of
corrosion on avionics equipment can cause serious
degradation or complete system failure. However, the
same amount of corrosion on aircraft exterior surfaces
might go unnoticed.
You can detect corrosion on the exterior of aircraft
or equipment visually. If you follow the scheduled
inspection requirements on a day-to-day basis, you
will ensure adequate detection of external corrosion.
It is harder to detect corrosion on the internal surfaces
of an aircraft because such surfaces are not easily
accessible. Thus., internal surfaces require special
attention.
Corrosion often progresses unnoticed by the
untrained technician. Therefore, the responsibility for
the detection and treatment of corrosion on the aircraft
is assigned to all work centers in each activity. This
ensures that sufficient knowledge is available to
perform all required inspections. Formal training in
corrosion control is a requirement for ALL
MAINTENANCE PERSONNEL. Through this
training, maintenance personnel are qualified to
perform inspections, corrosion damage repair, and
corrosion prevention. The corrosion control program
established by the Naval Aviation Maintenance
Program (NAMP) is an ALL HANDS participation
concept.
Aerodynamic efficiency is the primary
consideration of a manufacturer during the design and
production of an aircraft. The materials used for
construction are chosen for their weight-to-strength
ratio-NOT their corrosion-resistant properties. This is
one of the reasons your job as a maintenance crew
member is so important. When performing maintenance
on an aircraft, you must constantly look for surface decay
on all internal and external areas of the aircraft. You
should learn the corrosion-prone areas of your activitys
aircraft. Then, you can constantly inspect these areas
while performing maintenance. When a new aircraft is
delivered from the manufacturer, corrosion is already
present. Unless this corrosion is detected and treated, it
can become a serious problem that can endanger the
flight safety of the aircraft.
In addition to corrosion inspection of aircraft
surfaces, maintenance personnel must be equally
aggressive in preventing corrosion damage to aviation
support equipment (SE). This equipment keeps the
aircraft flying. The reliability and effectiveness of SE
also depend largely upon the structural soundness of
the metals that make up its parts. SE is used in a variety
of climatic and atmospheric conditions, ranging from
the hot, arid desert to cold, arctic regions. In addition,
the equipment is used in the salt-filled atmosphere of
coastal shore bases, islands, and aboard aircraft
carriers. In this environment, the sea winds carry 10 to
100 pounds of salt per cubic mile of air. These varying
environmental conditions promote corrosion and alter
the speed and intensity of its development. Severe
corrosion can cause components or systems to fail,
perhaps during critical demand times. When this
happens, replacements or corrective actions are costly,
4-1
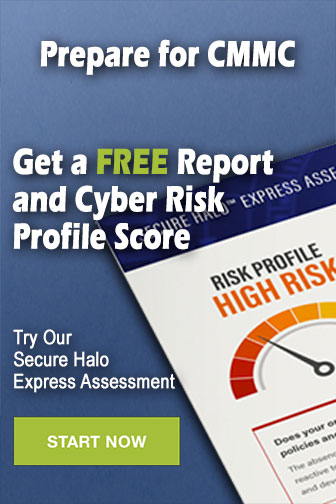