where they are converted into three-wire syncro
information signals. These signals are fed back to the
aircraft computer logic circuits to update the
computer and develop gimbal control data bits to
maintain the receiver head at the correct LOS.
If the system is operating in the position mode,
FWD mode, or computer track mode, and the operator
wants to quickly shift to the manual track mode, the
operator is able to do so by use of a manual override
function on the TTSC. When manual override is
initiated, a manual override command signal from the
TTSC is processed by the azimuth mode logic
module. This module sends a manual override signal
to the D/A converter. It also sends out manual track
command signals, as explained previously for manual
track mode. The FLIR system functions in the
manual track mode regardless of the position of the
control box mode select switch.
The manual track override signal disables the D/A
converter. It also sends a manual track mode status to
the aircraft computer logic to prevent the computer
from operating should the control box have computer
track selected.
Elevation Drive Subsystem
Figure 6-22 is the simplified block diagram of an
elevation drive subsystem. Compare figures 6-21 and
6-22. Notice they are the same except for the
elevation and azimuth labels on the modules. The
subsystems are the same because the servomechanism
elevation drive circuits operate the same and process
the same signals and develop the same drive signal as
the azimuth drive subsystem. The only difference is
that no tachometer feedback is used in the elevation
circuits, and all signals come from or go to elevation
circuits vice azimuth circuits.
In the FWD mode of operation, the elevation
circuits slew the receiver head to 4° (down tilt)
elevation. The azimuth circuits slew the receive head
to 0° azimuth. All other modes operate the same
except the receiver head is slewed in elevation instead
of in azimuth.
CS BITE Subsystem
The control servomechanism BITE subsystem
automatically determines whether a servo-system
failure is in the CS WRA or in the receiver-converter
WRA. Figure 6-23 is a simplified block diagram of
the CS BITE subsystem. For ease of signal tracing,
some of the modules have been duplicated at various
locations on the diagram. These modules, such as the
mode logic, have alphanumeric designators (A1, A2,
A3, etc.). However, the modules are all part of one
logic module. The alphanumeric numbers are used to
show where signals enter/leave a particular module.
A temperature sensor in the receiver-converter
monitors the gyro operating temperature. When the
gyros are operating properly, the sensor develops a
temp ready signal, regardless of which operational
mode is selected on the control box. The temp ready
signal is fed to the mode logic module (A1) of the CS.
The mode logic circuit outputs a rcvr ready signal to
the servo BITE module (B1). The rcvr ready signal
enables servo BITE (B1). When BITE is initiated on
the control box, a BITE initiate signal is received by
the servo BITE (B1) module from the power supply-
video converter BITE logic module. The BITE
initiate signal initiates a series of four test sequenced
as follows: fault isolate, BITE 1, BITE 2, and BITE
3. All tests are controlled by a 10-HZ clock in the
servo BITE module. Each test sequence takes 10 to
12 seconds to complete.
FAULT ISOLATE TEST. Initially (when rcvr
ready and BITE initiate are received), the servo BITE
module (B1) generates a BITE fault isolate signal and
a digital computer interface (DCI) fault isolate signal.
The BITE fault isolate signal goes to the following
modules:
azimuth position compensation (C1),
elevation position compensation (D1), mode logic
(A3), azimuth rate compensation (E1), and elevation
rate compensation (F1 ).
The signal enables all of
these modules and causes the azimuth position
compensation module (C2) and elevation position
compensation module (D2) to generate BITE motor
drive signals.
The DCI fault isolate signal goes to the decoder
storage module (for use in the BITE 3 test) and to
mode logic (A2). The DCI signal causes mode logic
to open the BITE relay drive line, de-energizing the
BITE relay (shown in the de-energized position).
Opening the relay removes azimuth and elevation
motor drive from the motors in the receiver-converter.
Instead, the azimuth and elevation heat sink motor
drive output is routed to the azimuth position
compensation module (C1) and the elevation position
compensation module (D1). The BITE motor drive
signals generated by the azimuth position
compensation (C2) and elevation position
compensation (D2) are routed by way of AZ POSN
and EL POSN lines to the azimuth rate compensation
(E1) and elevation rate compensation (F1),
respectively. The drive signals out of these modules
6-21
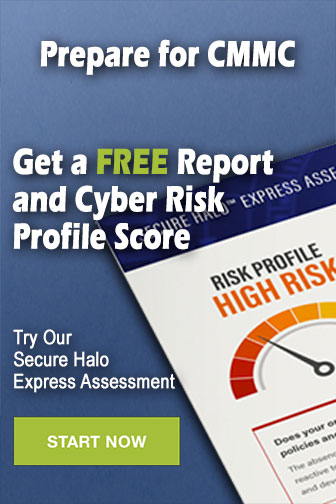