To perform the functional test proceed as
follows:
1. Place the supply valve control lever in the
ON position.
2. Place the diluter control lever in NORMAL
OXYGEN position.
3. Using an oxygen mask and hose assembly,
connect the hose to the quick disconnect. While
at ground level, the regulator will not supply
oxygen from the supply system to the mask. The
emergency pressure control lever must be used in
order to check out the oxygen supply function of
the regulator at low altitudes. (The emergency
lever is spring loaded at the NORMAL position,
and will return to NORMAL when released.)
Place the mask to your face with the regulator
in test mask position and inhale. Proper regulator
operation will be indicated by the flow indicator
assembly showing white during inhalation and
black during exhalation.
4. Hold the emergency pressure control lever
in the TEST MASK position and observe the flow
indicator. The flow indicator should be white,
indicating a flow through the regulator.
Upon completion of the functional test, secure
the regulator as follows:
1. Disconnect the mask from the supply hose.
2. Ensure that the emergency pressure
control lever returns to its NORMAL position.
3. Place the diluter control lever in the
100-percent position.
4. Place the supply valve control lever in the
OFF position.
If any discrepancies are found or suspected,
notify maintenance control. If repairs cannot be
made in the aircraft, replace the regulator and
forward the defective regulator to AIMD for
repairs.
CALENDAR/PHASED/SDLM
INSPECTIONS
You must remove the regulator to give it a
calendar, phased or SDLM (standard depot-level
maintenance) inspection. See applicable Planned
Maintenance System (PMS) publications for
specified intervals. In no case can the interval
exceed 231 days. Upon removing it from the air-
craft, the regulators are visually inspected and sent
to AIMD for bench testing.
Aircraft panel-mounted regulators that fail the
bench test must be repaired. Source, Maintenance
and Recoverability (SM&R) codes define repair-
ability of components and lowest level of
maintenance authorized.
Service Life
Oxygen regulators remain in service for as long
as they function correctly and do not require
excessive repair (exceeds 75-percent of original
cost of regulator). All silicone rubber parts are
replaced whenever a regulator is disassembled for
repair.
Bench Test
Bench tests are performed on aircraft panel-
mounted oxygen regulators prior to being placed
in service, and during the phase/calendar or
SDLM inspection cycle of the aircraft in which
installed. See applicable PMS publications for
specific intervals. The inspection interval must not
exceed 231 days. The regulators are also subjected
to a bench test if malfunction is suspected, and
after repair or replacement of damaged parts.
Bench tests are performed using Oxygen Sys-
tem Components Test Stand, Model 1172AS100,
in accordance with NAVAIR 13-1-6.4. Because
of the complexity of the 1172AS100 test stand,
it is essential that the operator become thoroughly
familiar with the test stand prior to performing
bench tests.
NOTE: Nitrogen supply cylinders used in
testing oxygen components are 80 cubic
feet and contain a maximum pressure of
2000 ± 200 psig. For tests requiring
pressures of 1800 psig, use highest available
pressure, but in no case can this pressure
be less than 500 psig.
Inward Leakage Test
By applying 9.0 inches (H2O) of suction to the
regulator outlet, you are testing the regulator to
be leaktight. If a leak is present, it could effect
other tests covered in the chapter. It could also
prevent the aircrewman from receiving 100-percent
oxygen by allowing ambient air to enter the
regulator.
To perform the inward leakage test, proceed
as follows:
1. Ensure that all test stand valves are closed,
then open N2 supply cylinder valve.
12-9
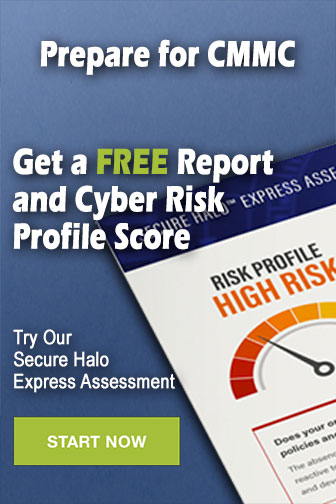