canopy to the next higher level maintenance
activity. This form must not be discarded. When
the repairs are done, the Canopy Damage Chart
is attached to the Parachute Configuration,
Inspection, and History Record.
NAVAL AVIATION MAINTENANCE
PROGRAM FORMS
The following forms used in the Naval
Aviation Maintenance Program (NAMP) are
applicable to parachute maintenance: VIDS/MAF
Form, Support Action Form, and DoD Single
Line Requisition System Document. Proper
completion of documents is essential to the
function of the program. Detailed instructions on
their use may be found in the Naval Aviation
Maintenance Program Manual, OPNAVINST
4790.2 (series).
RECORDING MODIFICATIONS
When a modification is performed on a
parachute assembly, you must record the assigned
technical directive code and modification code on
the Parachute Configuration, Inspection and
History Record. Other records must be completed
in accordance with OPNAVINST 4790.2 (series).
INSPECTIONS
The various times at which inspections are
performed on personnel parachutes are discussed
in the following paragraphs.
DAILY INSPECTION
A daily inspection should be performed on all
in-service parachute assemblies either installed in
aircraft or in ready issue rooms. The inspection
may be accomplished by line personnel, or by an
issue room custodian who has been checked out
by both the AME and PR shops and found
qualified. The inspection is performed in
accordance with the MRC for the equipment and
the requirements detailed in NAVAIR 13-1-6.2 for
the aircraft involved. It is done before daily flight
operations and is a visual in-place inspection. It
is also included in the special (7- or 14-day)
inspection.
The packaged parachute is inspected for
external evidence of damage. You should be
looking for wear or other evidence of physical
abuse. The assembly should also be checked for
stains, which may indicate contact with harmful
fluids or chemicals. Any stain should be con-
sidered harmful until the fluid that made it is
identified. Stains or discolorations may also be
caused by contact with a hot object. Heat can
seriously weaken the synthetic fabrics in parachute
assemblies. Another possible source of trouble is
exposure to ultraviolet radiation such as sunlight
or some types of artificial lighting. Any evidence
of damage or suspicious condition must be
reported to maintenance control.
SPECIAL INSPECTION
The special inspection is performed at intervals
of 7, 10, or 14 days, depending on the type of
aircraft. In-service parachute assemblies installed
in aircraft and in ready issue rooms are also given
this special inspection. This inspection includes
the integrated torso harness and quick attachable
harnesses. The daily inspection is included as part
of performing the special inspection. Assemblies
used for training, parachute rescue, pathfinding,
and reconnaissance teams, and those parachute
assemblies not assigned to a specific type of
aircraft are inspected every 14 days. It is done by
organizational level maintenance PR personnel,
such as yourself, and conducted only under
adequate lightning conditions.
This inspection includes, but is not limited to,
emergency aircraft escape assemblies and/or
systems, as well as assemblies used for pre-
meditated free-fall or static line parachute
descents. The reserve (emergency) parachute,
which may form a part of a training-type, troop-
type, or a test assembly, is also inspected.
Parachute assemblies are not opened for the
special inspection or for the daily inspection. If
you find or suspect any damage or contamination,
notify maintenance control. When you complete
the special inspection, enter your full name, rate,
and current date on the Preflight/Daily/Turn-
around/Postflight Maintenance Record Card.
ACCEPTANCE (ORIGINAL ISSUE)
CALENDAR/PHASED/CONDITIONAL
INSPECTIONS
The acceptance (original issue)/calendar/
phased/conditional inspection is performed at the
lowest level of maintenance possible. These
inspections include, but are not limited to, aircraft
emergency escape assemblies and/or systems.
1-22
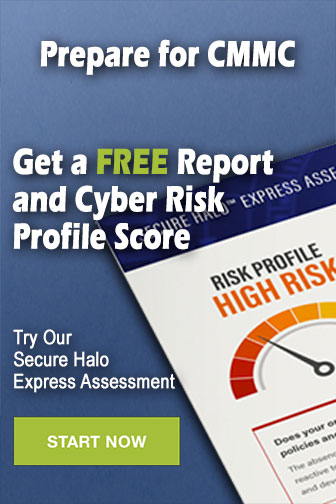