Also include the Parachute Configuration,
Inspection, and History Record and any reference
information or documents that would have a
bearing on a technical investigation. If the
aircrewman sustained fatal or serious injuries
during the escape or recovery sequence, include
photographs of the parachute, ejection seat, and
other components at the scene of the impact.
Ensure the proper shipping tags and labels are
attached to all equipment and the shipping
container. If pyrotechnics or explosives are in the
package, it should be noted on the outside of the
c o n t a i n e r .
PROCEDURES FOR PRELIMINARY
TESTS AND INSPECTIONS
When you are assembling a parachute for an
original issue inspection or performing a normal
calendar repack, you will have to do some
preliminary test and inspections that are common
to all personal parachutes. These inspections and
tests are discussed in the following text.
RIPCORD PULL TEST
Parachutes must be given a ripcord pull test
before being unpacked for inspection. The
maximum pull force that you may use is 27
pounds. If you go over 27 pounds, the ripcord
pins, cones, and grommets must be checked for
bends, dents, and roughness, and make sure that
the ripcord cable moves freely in the housing.
Inspect the housing for sharp bends or dents and
replace any damaged parts. Silicone spray may
be sparingly applied to ripcord parts. Make sure
that ripcord pins are properly positioned before
testing. All assemblies with metal ripcord handle
clips require an additional test. To do this, use
a straight pull to remove the handle from the clip;
this will require 10 to 20 pounds of force. If not
within limits, use pliers to adjust the clip.
SERVICE LIFE CHECKS
Testing the ripcord opens the container. If the
assembly includes explosive devices, they must be
deactivated at this time. The canopy is then placed
on the table with the nameplate up. If the
parachute is being placed in service, the date is
stenciled on the parachute canopy on the
nameplate gore directly below the nameplate.
For a periodic inspection, you should verify
the nameplate data against the Parachute
Configuration, Inspection, and History Record,
or History Card. If the service life dates listed
on the history card are in accordance with the
Maintenance Requirement Cards, NAVAIR
13-600-4-6-3, check their expiration dates against
the current date of inspection. Items that have
reached service life limits must be replaced. Items
that will become overage after the assembly is
repacked may remain in service until the next
inspection date of the complete assembly. An
exception to this are the explosive devices, which
must be replaced if their expiration date will be
reached before the next inspection.
REPLACEMENT OF PARACHUTE
ASSEMBLIES AND SUBASSEMBLIES
Not all the components of a parachute
assembly come to the end of their service lives at
the same time. After a parachute has been in
service for some time, some of the components
or subassemblies will have to be replaced in the
course of the periodic inspections.
If you find an assembly or subassembly that
has reached the service/total life limit, it should
be returned to supply for appropriate disposition
according to current supply instructions. Before
turning an overage assembly in to supply, you
should remove all serviceable ready for issue (RFI)
subassemblies. You should carefully inspect all
nylon webbing and cloth on items to be salvaged.
Dirt, oil and grease greatly weaken these
materials. All fabric items salvaged must have date
of manufacture and date placed into service
markings verified prior to disassembly. Cartridges
used on cartridge-actuated parachutes are to be
handled, shipped, stored or disposed of in
accordance with NAVAIR 11-100-1. When an in-
service parachute does not have a start of service
date, the service life from date of manufacture
expires as follows: in 7 years for emergency use
parachute assemblies; in 10 years for troop and
training assemblies.
CONTAMINATION INSPECTION
Contamination of a parachute canopy or an
assembly could result in the malfunction of the
complete assembly. It is very important that you
be able to recognize a harmful stain. All parachute
assemblies must be carefully inspected for the
following types of contamination:
1. Acid/alkaline
2. Salt water
1-24
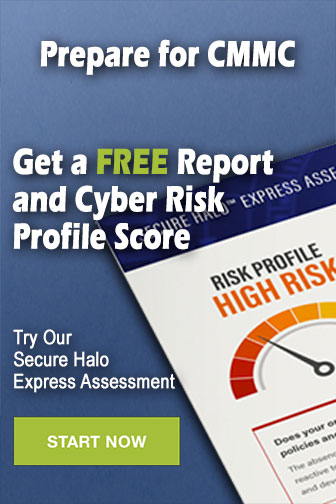