Performing technical research and preparing
supply requisitions
Delivering material to customers
Monitoring turn-in of repairable components due
from both O- and I-level maintenance activities
Maintaining the local repair cycle asset (LRCA)
storage areas and providing listings of available
components to customers
Establishing, maintaining, and replenishing
pre-expended bins (PEBs) and providing PEB
listings to customers
Coordinating with the AIMD to originate
customer service requests with the NADEP
Initiating local expeditious repair (EXREP)
requests
Maintaining awaiting parts (AWP) storage areas
and establishing requisitions and follow-up
procedures for required AWP piece parts
Expediting high-priority requisitions
Measuring supply response time
For detailed procedures for the responsibilities of each
unit, refer to OPNAVINST 4790.2.
LOCATION
The ASD/SSC should be located adjacent to
maintenance areas to improve maintenance/material
support coordination. The physical location of the
SSC/ASD may vary according to local geographic and
facilities layout.
HOURS OF OPERATION
All the functional areas of the ASD/SSC must be
manned and operational during the operating hours of
all maintenance activities being supported. When
maintenance is being performed 24 hours a day, supply
support is required 24 hours a day. Manning levels
during other than normal working hours must be
consistent with the support requirements and
requisitioning processing standards.
MEANS OF RECEIVING REQUISITIONS
In manual processing, ASD/SSC may receive
requisitions on various forms. These forms include DD
Form 1348 (6 pt and DD Form 1348-6. ASD/SSC may
also receive requisitions via message.
In automated activities, ASD/SSC receives
requisitions electronically via computer terminals.
RESPONSE STANDARDS
Maximum elapsed response times are established
for the issue of items available in local supply stock or
furnishing the customer with requisition status on an
automatic basis for not-carried (NC) or not-in-stock
(NIS) items. Response time starts when the requirement
is placed in the SSC/ASD and stops when the requested
material or status is received at the delivery mint.
Chapter 8 of this TRAMAN shows these time standards.
Response time should be individually measured and
maintained on a monthly basis for review by the supply
officer.
The NALCOMIS activities can print the Issue
Response Time Analysis Report through conversation
code N692. The user can specify the ORG code, Project
code, and urgency of need designator along with
inclusive dates for the report. This report summarizes
the issue response time by Project code within Type
Equipment code, within organizational code, and within
issue group.
STATUS LISTINGS
Daily mechanized listings that provide complete
supply status for all NMCS/PMCS and anticipated
NMCS are provided by the program management unit
(PMU) to both the O- and I-level maintenance activities
in sufficient quantity to ensure adequate distribution.
Data is sequenced to expedite the daily validation
process. As a minimum, the listings contain the
following information:
. Document number
. Cognizant symbol (COG), material control code
(MCC), national stock number (NSN), and special
material identification code (SMIC)
Unit of issue and quantity
Project and priority
Bureau number
Nomenclature
Status/Routing
submitting status
Identifier code (RIC) of activity
9-4
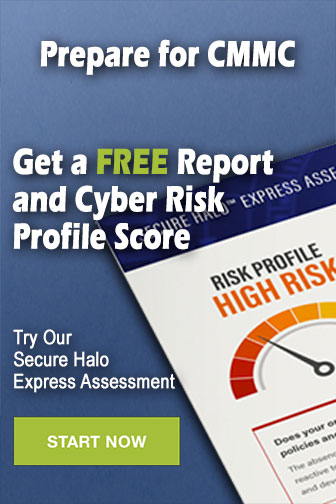