Swing check valves use a disk that is attached to
the valve body by a pinned hinge and is closed by
gravity during a no-flow condition. This type valve is
sometimes designed with a spring to assist closing the
valve. Pressure caused by flow forces the hinged disk
up to open the valve. But, pressure in the opposite
direction will force the hinged disk back on its seat to
close the valve.
The proper positioning of the valve, with refer-
ence to the horizontal, is very important to ensure
proper check valve operation. Since the downward
force of gravity is necessary for proper operation, a
check valve installed upside down or at any angle
other than horizontal may not function as intended.
Also, since this valve allows flow in only one direc-
tion, it must be installed correctly. Most check valves
will have a flow direction arrow on the body. If no
arrow is visible, the inlet side of the valve will be the
side with the hinge pin.
VALVE MAINTENANCE
All valves require proper care and maintenance,
as does other more complex equipment, to ensure they
are kept in optimum working order. The principle
difficulties encountered with valves are leakage past
the seat and disk, leakage at the stuffing box, sticking
valve stems, and loose valve disks.
Losses due to leakage that is not corrected mount
up considerably over time. For example, over a period
of a month, a small 1/32 inch hole would waste 69.552
cubic feet of air at 100 psi, 3,175 pounds of steam at
100 psi, or 4,800 gallons of fuel at 40 psi. The ABF
should know how to prevent and correct these faults.
Valve Leakage Causes
and Remedies
Valve leakage, generally caused by failure of the
disk and the seat to make close contact, may result
from any of the following:
Foreign substances, such as scale, dirt, or heavy
grease lodged on the valve seat may prevent the disk
from being properly seated. If the obstructing material
cannot be blown through, the valve has to be opened
and cleaned.
Scoring of the valve seat or disk, which may be
caused by erosion or by attempts to close the valve on
dirt or scale, results in leakage. If the damage is mini-
mal, the valve may be restored to proper working order
by grinding. If the damage is more extensive, the valve
must be reseated and then ground.
A warped disk may result if the guides fit too
tightly, if the spindle guide is bent, or if the valve stem
is bent. Using a valve disk or body that is too weak for
the purpose for which it is used permits distortion of the
disk or seat under pressure. If this occurs, replace the
valve.
Packing Gland Leakage
Packing gland leaks can be remedied by tighten-
ing the gland or repacking it. But, the gland must not
be tightened nor packed so tightly that the stem binds.
If the leaks persist after either or both of the remedies
are applied, a bent or scored valve stem may be the
cause.
Packing for the valve may be either of the string
type or of the ring type. String packing is ordinarily
used for small valves in low-pressure systems. Ring
packing is used for large valves and for all high pres-
sure valves. When replacing the packing on any type
of valve, be sure to use the correct size and type. The
packing must be large enough to fill the space be-
tween the valve stem and the packing box. It also must
be made of material that is suitable for the pressure
and temperature to which it will be exposed.
To pack a valve with string packing, place succes-
sive turns of packing in the space around the rod.
Bevel off the ends of the packing to make a smooth fit
and tighten the packing gland nut or the bonnet nut to
compress the packing. String packing should always
be wound in the same direction as the gland nut is to
be tightened so tightening the nut does not cause the
packing to fold back upon itself. To pack a valve with
ring packing, cut the ends of the rings square and even
so they make a level butt joint. Be sure to stagger the
joints in successive rings.
In some gate, globe, and one-way check valves,
the packing gland may be repacked under pressure,
when necessary. These valves are constructed with
the stem back-seated against the bonnet when the
valve is wide open. High-pressure valves are provided
with a pressure leak-off connection. The pressure
leak-off connection is sealed to the outside with a pipe
plug. Extreme care should be taken to see that the
valve is firmly back-seated before the plug is re-
moved. Normally, repacking valves under pressure
is NOT done by an ABF. If a valve must be re-
packed under pressure, ensure ALL SAFETY
PRECAUTIONS are followed.
4-22
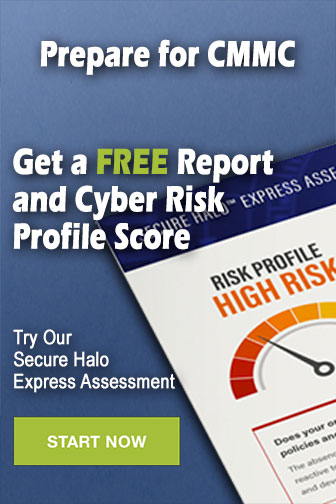