AVIATION
CHAPTER 4
MATERIAL MANAGEMENT
The unique characteristics of todays Navy, for the
most part, determine the nature and size of its supply
management. Supply management has adapted itself to
the changing material requirements and advancing
technologies. Supply system procedures have also
adapted to respond to the changing operational
requirements,
This chapter will help you learn the principles and
procedures for managing aviation material. You will
learn the procedures for issuing an Aviation
Consolidated Allowance List (AVCAL) and Shore
Consolidated Allowance List (SHORCAL) to an
activity. You will also learn the procedures to properly
manage the AVCAL and SHORCAL.
THE NAVY SUPPLY SYSTEM
The term Navy supply system describes that system
under the direction of the Commander, Naval Supply
Systems Command, consisting of inventory managers
and stock points, with primary functions to provide
material to the Operating Forces of the Navy.
The major responsibility of the Navy supply system
is to provide material in support of the operation and
maintenance of aeronautical equipment. Every effort
will be made to have material located when and where
it is needed. The intent is to make the relationship
between the supplier and the user as simple and
uncomplicated as possible within the boundaries of
logistics directives published by higher authority.
SUPPLY SYSTEM MANAGEMENT
The Navy supply system is part of the total federal
supply system. It procures, maintains, and distributes
equipment, repair parts, and consumable inventories to
Navy customers. he basic responsibility for providing
supply support to meet user needs is the function of
naval inventory control points (NAVICPs). The
cognizant systems command and the users determine
the individual supply support measures of ashore and
afloat units.They also determine the range and depth
of items to be carried and position inventories at those
designated activities.
The Naval Inventory Control Point-Philadelphia
(NAVICP-Phil) is the primary inventory manager of the
aeronautical items used in the Navy. Commonly, the
senior AK is involved in managing aeronautical
materials in the retail level. Technical aviation material
consists of material and spare parts for aircraft, power
plants, avionics, electrical and meteorological
equipment, safety equipment, and support equipment
(SE) both common and peculiar. All of these items are
composed of consumable and repairable aviation
materials. The repairable items are also referred to as
Aviation Depot Level Repairable (AVDLR) or Depot
Level Repairable (DLR). AVDLR components
represent the most significant dollar investment in the
entire aeronautical item inventory. Improved
management of these components is essential to the
increased readiness of the operating forces and to the
reduction of support costs.
The NAVICP-Phils material mission is the
program support of weapons systems, aeronautical
equipment, and components under the design,
engineering, and configuration control of the Naval Air
Systems Command (NAVAIRSYSCOM). Certain
items required in support of NAVAIRSYSCOM
material programs may be under the management
cognizance of several ICPs; however, program
information is provided by NAVICP-Phil to these ICPs
to enhance the supply support.
MANAGEMENT OF REPAIRABLES
A repairable is an item that, when unserviceable,
normally can be economically restored to a serviceable
condition through repair procedures. Repairable are
grouped as field level repairable (FLRs) or depot level
repairable (DLRs). The criteria used to categorize an
item as FLR or DLR is based on the lowest level
authorized to condemn the item.
The FLRs are condemned and disposed of at the
field level. The material control code (MCC) D is
assigned to identify FLRs. The inventory levels for the
FLR are computed in the same manner as for
consumables.
The DLRs are items that can be economically
repaired at depot level (D-level) maintenance if it is
4-1
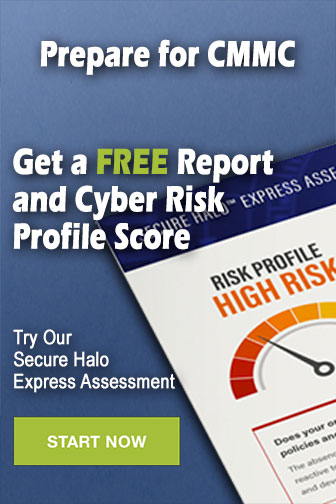