price. The customer will be balled for the FLR issued
and will not be credited for NRFI turn-in.
The NRFI FLR is disposed of according to the
MRIL. Stock replenishment for FLRs may be obtained
from the purpose code A stock or from the supporting
supply source. Refer to NAVSUPINST 4440.159 for
detailed procedures for FLR transactions.
DEPOT LEVEL REPAIRABLES (DLRs)
The DLRs are repairable items for which the
condemnation should be made at the depot level. These
items may also be repaired at the organizational or
intermediate level as determined by the assigned
SM&R code. Depot level repairable are further
categorized as described in the following paragraphs.
. Aviation Depot Level Repairable (AVDLRs)
are DLRs under the management of the Naval Inventory
Control Point-Philadelphia (NAVICP-PM). Selected
repair or maintenance of AVDLR components can be
accomplished at the intermediate maintenance activity
(IMA). Unserviceable AVDLRs that were determined
to be beyond capability of maintenance (BCM) at the
IMA must be shipped to the depot repair facility.
. Non-AVDLRs are DLRs under the management
of the Naval Inventory Control Point-Mechanicsburg
(NAVICP-Mech). Unserviceable non-AVDLRs are
shipped to a depot repair facility when determined to be
BCM at the IMA.
. NSA DLRs are Defense Business Operations
Fund (DBOF) owned DLRs under the management of
NAVICP-Phil or NAVICP-Mech. The NSA DLRs are
carried in stores account 51000.
. Appropriation Purchase Account (APA) DLRs
are those items identified by an even number
cognizance (Cog) symbol and managed by
NAVICP-Phil or NAVICP-Mech. These DLRs are
carried in stores account 52000.
MANAGEMENT PROGRAMS FOR
AVIATION REPAIRABLE
Several management programs for repairable have
been established within the aviation supply system to
enable the IMs to maintain control and to make sure
unserviceable components are repaired in a timely
manner. Some of these special programs are discussed
in the following paragraphs.
OPERATIONAL SUPPORT
INVENTORY/FIXED ALLOWANCE
Weapons systems are supported under the
operational support inventory/fixed allowance concept.
Refer to NAVSUPINST 4440.160, FASOINST
4440.15, and FASOINST 4440.16 for detailed
procedures. A negotiated firm allowance of repairable
assets may not be exceeded without NAVICP
authorization. Strict one-for-one exchange discipline
between O- and I-level maintenance activities and the
supply department must be maintained. Off-station
requisitions must not be submitted before the item is
confirmed as beyond capability of maintenance (BCM),
except when the item is listed in the consolidated remain
in place list (CRIPL). The NAVICP maintains visibility
of stock records of fixed allowance repairable through
the transaction item report (TIR) from activities
assigned as TIR sites. Storage of fixed allowance assets
is authorized at any ASD/SSC location within the
operating site. Normally, the storage site is referred to
as the LRCA storage unit.
INTENSIVE REPAIRABLE ITEM
MANAGEMENT (IRIM) PROGRAM
The NAVSUP Instruction 4419.4 describes the
IRIM program at the inventory control points in detail.
This program was established to standardize previously
existing programs for intensive management of high
cost, critical aviation, and shipboard repairable items.
For aviation repairable, the IRIM program replaces the
intensive closed-loop aeronautical management
program (I-CLAMP). The implementation of the IRIM
program is designed to resolve problems with
availability, reduce backorders, improve repair
turn-around time (RTAT), and improve carcass returns.
You can also refer to ASOINST 4440.99 concerning the
IRIM program.
COMPONENT REPAIR PROGRAM
The primary objective of the aeronautical
component repair program is improved readiness
through the return of all repairable components to the
operating forces with the least expenditure of material,
manpower, and money. The scope of the component
repair program is virtually unlimited since it ranges in
depth from minute adjustment to complete repair of
selected components. The program encompasses those
functions performed by the O-, I-, and D-levels of
maintenance during the overhaul, repair, check, test,
certification, modification, or manufacturing processes.
4-5
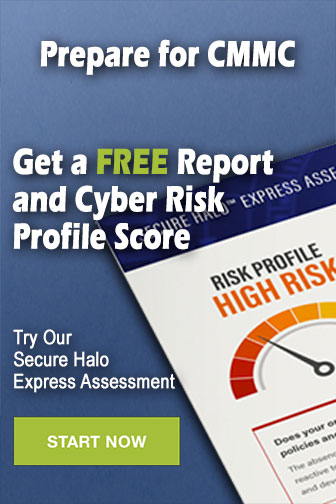