maintenance data system (MDS) data supplied by the
Naval Sea Logistics Center and will be made after the
repairs have been accomplished by fleet maintenance
personnel.
Warranty identification depends upon whether the
material is contractor-furnished equipment (CFE) or
government-furnished equipment (GFE).
Aircraft and engine warranties cover the basic
aircraft or engine and the CFE. The warranty markings
and information are documented in the Miscellaneous/
History section of the aircraft logbook or engines
Aeronautical Engine Service Record (AESR).
The GFE items have a distinct and separate
warranty. The warranty information is marked on the
equipment and on any associated record cards. The
work unit code assigned to GFE is usually 51000 or
higher.
Naval Aircraft Tire Rebuilding Program
The NAVICP-Phil is responsible for centralized
contracting for the rebuilding of naval aircraft tires.
The NAVICP-Phil is also responsible for the complete
administrative control of the rebuilding program. The
cost of rebuilding a tire approximates to 36 percent of
the cost of the new tire. Full participation of all
activities in the rebuilding program will save a
considerable amount of dollars.
It is the policy of the Navy that all aircraft tires are
rebuildable. However, there are selected types of tires
that are exempt from the rebuilding program because of
technical or economic reasons. The types of tires that
are not rebuildable are listed in the enclosure of
FASOINST 13421.1.
The NAVICP-Phil is also responsible for the
funding, allocation of rebuildable tires for rework and
service, establishment of shipping procedures, and
shipping logistics.
The user activities must exert the effort to generate
repairable tires.
Strict inspection and screening
procedures must be performed in the determination of
tires to be rebuilt. Inadequate screening of tires can
result in shipping rebuildable tires to a Defense
Reutilization and Marketing Office (DRMO) as scrap.
In some cases, tires that should be marked as scrap are
shipped to the rework facility.
The elimination of age shelf/service limits on
aircraft tires, as well as the elimination of maximum
rebuild level occurrences, makes good stock control and
issue practices necessary. For both new or rebuilt tires,
the oldest tires must be issued first. The date of
manufacture is basis for issuing the tires. The date of
rebuilding must not be used for issuing procedures. The
tires are marked with the manufacture date included
with the serial number. The serial number consists of a
maximum of 10 characters (alpha or numeric). The first
four characters is the date of manufacture in the form of
a Julian date. Tires that are manufactured before this
method have manufacturing dates separate from the
serial number and are identified by month and year, or
day, month, and year.
The system of color coding tires to indicate the
manufacture date helps in the identification and issue
processing. A strip of colored tape imprinted with
manufacture date, and diamond shape to designate
rebuilt tires, is applied around the circumference of the
tire.
Tires that have been removed from aircraft and
returned to the tire shop must be thoroughly inspected
by a qualified inspector to determine their disposition.
The appropriate condition code tag must be affixed to
the tires as a result of the inspection. Rebuildable tires
must be assigned condition code F and condemned tires
with condition code H. Tires identified with condition
code H will be shipped to the nearest DRMO or
property disposal officer. Ship tires in condition code
F according to the MRIL or via ATAC Hub.
FLEET READINESS ACTION GROUP
(FRAG)
The FRAGs are fictional units established within
each naval aviation depot. The FRAG is assigned
responsibility to help the fleet achieve maximum
aircraft readiness. The FRAG uses technical and
logistics resources available at a NADEP using
industrial and engineering resources in resolving
critical supply support problems on an exception basis.
The FRAG operations are limited to the weapons
system supported by the particular NADEP, CFA, and
depot repair point. When critical maintenance/material
problems cannot be solved using normal procedures,
contact the FRAG by naval message or telephone.
NAVAL INVENTORY CONTROL
POINT-PHILADELPHIA RECLAMATION
PROGRAMS
The overall NAVICP-Phil reclamation program
consists of several subprograms. These programs are
differentiated by the item undergoing reclamation (for
example aircraft, engines, and so forth).
4-10
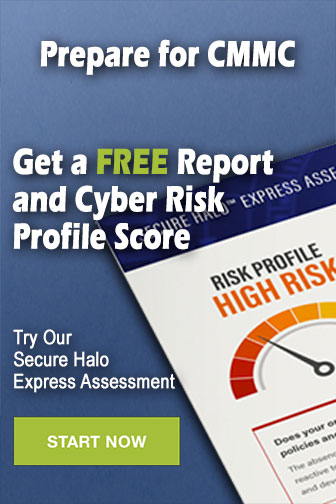