The avionics division officer is responsible for a
comprehensive training program for supply and
maintenance personnel and ensures compliance with the
requirements outlined in the Electrostatic Discharge
Control Handbook for Protection of Electrical and
Electronic Parts, Assemblies and Equipment,
DOD-HDBK-263, and the Electronic Assembly Repair,
Standard Maintenance Practices Manual, N A
01-1A-23, work package 005 for all avionics personnel
and others who come in contact with ESD sensitive
assemblies/devices.
All printed circuit assemblies/
microcomponents are considered to be ESD sensitive
while being handled, packaged, repaired, and
transported. Guidance and direction for the
identification, handling, and protection of ESD sensitive
components should be followed according to NAVSUP
Instruction 4030.46, and appropriate TYCOM
instructions. Supply Afloat Packaging Procedures,
NAVSUP P-484, details the proper methods and
required materials used in packaging ESD sensitive
components for storage and shipment.
Personnel safety cannot be overstressed in this
program. In the past, technicians have always been
isolated from electrical shock by nonconductive rubber
mats. In ESD safe areas, these nonconductive mats have
been replaced with conductive material/devices through
which the technician is attached by a soft ground (a
connection to ground through an impedance sufficiently
high enough to limit current flow to safe levels for
personnel), normally 5 milliamperes.
NOTE: Impedance is the opposition to current
flow in an alternating current circuit.
Impedance needed for a soft ground is dependent
upon the voltage levels that could be contacted by
personnel near the ground. The practice of handling
SRAs with power applied is strictly prohibited.
Strict compliance with these procedures must be
followed by supply personnel who receive, store, ship,
and issue ESD-sensitive components.
Engineering Investigation (EI) Program
The EI program was established under NAVAIR
direction to conduct technical engineering
investigations on failed materials. These investigations
include identifying causes and contributing factors and
recommending required corrective actions.
PURPOSE. The EI program is applicable to all
aircraft and weapons systems, subsystems, equipment,
components, related support equipment (SE), special
tools, and fluids/materials used in the operation of the
equipment. The EI program accomplishes the
following objectives:
l Provides an investigation process to determine
the cause and extent of fleet-reported material failures.
l Supports the investigation of material associated
with aircraft mishaps, lightning strikes, electromagnetic
interference, and stray voltage problems.
l Provides for investigation of components
rejected through the Joint Oil Analysis Program
(JOAP).
l Supports the scheduled removal component
(SRC), assembly service record (ASR), equipment
history record (EHR), and module service record(MSR)
programs by providing for the investigation of
high-time and on-condition components/assemblies to
confirm, revise, or initiate component/assembly
operating times.
. Provides for engineering assistance relating to
any fleet material problem.
. Supports the mandatory investigation
requirements for activated aircraft escape systems as
listed in OPNAV Instruction 3750.6.
Three different types of EIs may be conducted.
They are the disassembly and inspection, material
analysis, and engineering assistance.
RESPONSIBILITIES OF THE ORIGINATING
ACTIVITY. The activity must submit the EI request
under one or more of the following conditions:
. Safety is involved
. Additional technical or engineering information
is required to complete an aircraft mishap investigation.
l Aircraft readiness is seriously impaired because
of poor material reliability.
. A component is rejected through the JOAP after
authorized repairs are attempted and exhausted at the
organizational and intermediate maintenance level.
l When directed by higher authority.
The originating activity must submit the EI request
by routine precedence message within 5 working days
after discovery of the deficiency. However, if the EI
request is combined with a Hazardous Material Report
(HMR), follow the reporting criteria for the HMR.
NOTE: Refer to OPNAVINST 4790.2 for HMR
procedures.
4-7
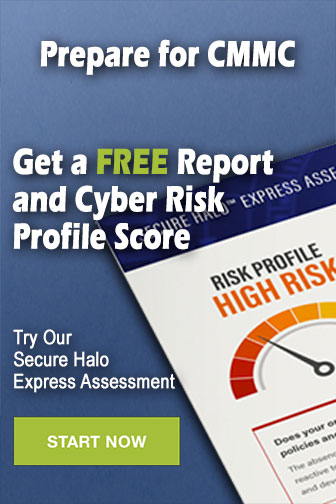