a result of the RIP, some allowances at an operating site
may or may not get adjusted. Increases in depth and
additions to the range to the ships allowance are
implemented during the re-AVCAL.
Preliminary AVCAL Aids
The Naval Inventory Control Point-Philadelphia
(NAVICP-Phil) forwards the preliminary AVCAL
review aids to the applicable ship and cognizant
TYCOM 45 days before the scheduled conference date.
AVCAL Quality Review Conference (AQRC)
The NAVICP-Phil convenes the conference to
negotiate the allowance requirement of the operating
site. The information in the sites maintenance data
collection system is the primary element in negotiations
of repairable items.
The information includes the
number of items processed as BCM, items repaired, and
the TAT of repairs.
The NAVICP-PMI adjusts the
preliminary requirement levels to reflect the negotiated
allowance. Authorized changes will be incorporated in
the final AVCAL products that are forwarded to the
operating site.
NOTE: The ACR-F is used to request an increase
or decrease in allowance after the re-AVCAL.
Miscellaneous Requirements
Other OSI requirements include the industrial
support package (ISP) and the supplemental aviation
spares support (SASS).
The ISP is designed to provide an 8-month range
and depth support for an aircraft carriers LRCA and is
currently incorporated in the community SAVAST.
The SASS is supplemental and not additive to the
operating sites AVCAL quantity. These requirements
are based on several factors, as follows:
The level of repair
The number and type(s) of aircraft to be
supported
Predicted removals
The flying hours expected over an endurance
period
LEVEL OF REPAIR. OverhauI, repair, and
maintenance of aeronautical material and weapons
systems are performed within the broad guidelines of
three levels of maintenance.
They are the
organizational, intermediate, and depot levels. A list of
aircraft maintenance functions classified to the
maintenance levels is provided in OPNAV Instruction
4790.2. It is important that you have a thorough
knowledge of the maintenance that can be performed
by your particular activity.
Organizational Maintenance. The classifica-
tion of O-level maintenance is applied to those
maintenance functions normally performed by an
operating unit on a day-to-day basis of its own
operation. O-level maintenance can generally be
grouped to include aircraft inspections: servicing,
handling, removal and replacement of defective parts
and components; aircraft service changes and
modifications; and necessary recordkeeping and reports
peculiar to O-level maintenance.
Intermediate Maintenance. The I-level
maintenance includes the repair and test of aircraft
components and items requiring shop facilities and/or
skills and equipment not available in O-level
maintenance activities.
Incorporation of aircraft
service changes and modifications beyond O-level
capabilities is also a function of I-level maintenance.
Depot Maintenance. The classification of
D-level maintenance is applied to those functions
performed at industrial-type activities such as naval
aviation depots (NADEPs). The NADEPs are normally
located at major air stations and perform overhaul and
major rework on aircraft, engines, and components on
a scheduled basis as directed by NAVAIR. They also
perform a customer service program for nonscheduled
overhau/repair on components to satisfy not mission
capable supply (NMCS) requirements.
Change of Maintenance Level. When the
maintenance level designation of an activity is changed,
the range of supporting repair parts carried in stock as
well as the equipment is involved.
A change to a higher level of maintenance requires
additional spare repair parts. It is also possible that the
supply level could be changed at the same time. Each
NAVAIR outfitting and allowance list in use is screened
carefully to make sure that all items required to support
the higher level are procured.
A change to a lower maintenance level involves
almost the same steps except in reverse manner. Many
of the items required for support of a higher level are
no longer required or allowed. Therefore, they must be
returned to the supply system, and the equipment will
normally be transferred to another activity for use.
4-21
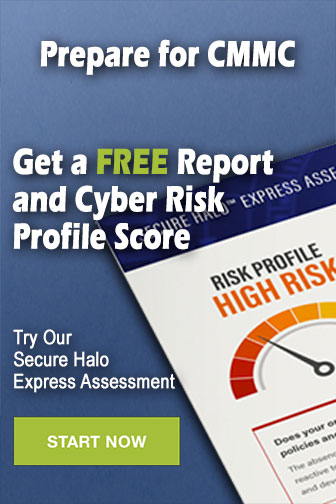