Table 4-1.-Constrained Turn-Around Time
. The item is locally repairable at the
organizational or intermediate level of maintenance.
l Constrained TAT is used in the computation (see
Table 4-1). The TAT is the number of calendar days
between removal of the item for processing through
repair cycle until it is available for reinstallation.
In computing the total average TAT for each NIIN,
use the lower figure of the actual experience or
maximum allowed time for each repair element. After
summing the individual elements, the total NIIN
average will be constrained to 20 days. The constrained
average daily NIIN TAT is used in the calculation of
LRCR values.
To determine the LRCR quantity, use the
computation formula and Poisson distribution table
(part of enclosures) in FASOINST 4441.15 or
FASOINST 4441.16.
SUMMARY
In this chapter, we discussed the Navy Supply
System echelons and their functions for managing
aeronautical materials in the Navy. Aeronautical
material is composed of consumable and repairable
items. We discussed the difference between these
categories of material and the procedures used to
determine the activitys stocking levels for each
category.
The primary inventory manager of aeronautical
materials in the Navy is the Naval Inventory Control
Point-Philadelphia.
The repairable items are
categorized as field level repairable (FLR) and aviation
depot level repairable (AVDLR). The AVDLR items
represent the most significant dollar investment in the
aeronautical inventory.
Therefore, strict inventory
control is required to manage these items.
The activities that are required to provide supply
support to aircraft and aeronautical equipment will be
outfitted with items for stock. The designated activity
is outfitted through the AVCAL/SHORCAL process.
After the AVCAL/SHORCAL process, any increase or
decrease to the allowance quantity must be submitted
to the NAVICP on the Allowance Change
Request-Fixed (ACR-F) form. The FLRs may be
carried in purpose code W or L of an activitys fixed
allowance. The FLRs that are excess to the authorized
allowance are carried in A purpose code. Ships carry
FLRs under stores account 51000 pending issue to the
customer. The ownership of AVDLR items relate to the
stores account they are carried under. These stores
accounts could be the DBOF, APA, contractor
supported, and end-use ashore or afloat.
We discussed the different Navy management
programs for AVDLR items. These programs provide
specific procedures in inventory management,
scheduling, repair, carcass tracking, reclamation, and
support of AVDLRs.
Managing repairable material has become more
significant in todays Navy. The activities must ensure
that procedures for processing transactions are being
followed. Since the number of AVDLR items in the
Navy has increased, intensive management procedures
are required. The inventory management and carcass
tracking programs provide the necessary procedures in
support of the AVDLR.
We discussed the carcass tracking and the
Advanced Traceability and Control (ATAC) programs.
The carcass tracking program includes shipment of
retrograde, maintaining carcass tracking records
(CTRs), carcass tracking follow-up inquiry from
NAVICPs, replies from shipping activities, and billings.
The follow-up inquiry documents must be processed
within the prescribed time frame to prevent additional
billing from the NAVICPs.
To prevent the duplication of effort and to ensure
currency of information, certain paragraphs in this
chapter refer you to the reference(s) that describe the
subject in detail.
4-27
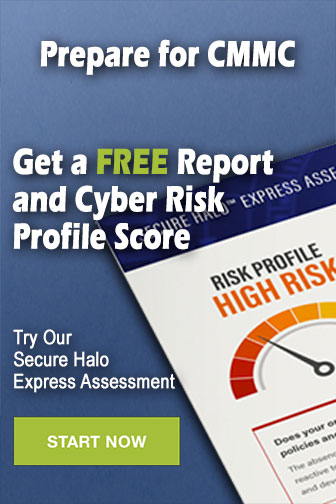