CHAPTER 5
INVENTORY MANAGEMENT
The Navy supply system has two primary
partsinventory management and physical
distribution. In this chapter we describe the
information you should know about inventory
management.
Aviation Storekeepers are assigned to billets in
Navy stocking activities. These are activities afloat or
ashore that carry materials in inventory stores account
for their own use or to support other activities. As a
senior AK, you should familiarize yourself with the
procedures for managing stock items in your activity.
This chapter will help you understand the practices and
procedures applicable to material custody and
inventory management. You should also learn the
procedures for conducting physical inventory and
reconciling inventory results.
Inventory management functions include deciding
what items and how many of these items should be
stocked. The function includes deciding where to store
the items so they will be close to the likely users. It also
includes tracking the material from the time it is ordered
until it is issued. Inventory management is mainly done
at the naval inventory control points (NAVICPs).
A perfect inventory management enables every
material requirement to be satisfied from stock within
the required time frame. Although this is the ideal result
for each material request, this goal is often not achieved.
To achieve this goal is to put every item needed to
support all aircraft and equipment in the stock
inventory. However, this will cost a large amount of
money, especially for those items that are seldom used.
To provide supply support and keep the inventory cost
to a minimum, the projected customer demand is used
as the foundation of the federal inventory management
system. (NOTE: Demand is any request for an item.)
To properly invest funds, any item without a projected
demand is not stocked, or is removed (purged) from
stock.
The Navy inventory management activities are
those organizations assigned as primarily responsible
for managing assigned groups or categories of supplies.
These activities are classified into two groups as
follows:
1. Navy commands whose principal mission is
Navywide program management of weapons
systems/major items. These are the Hardware Systems
Command (HSC), Project Offices, the Navy Training
Systems Center, and the Military Sealift Command.
2. Naval Inventory Control Point (NAVICP)
under the Naval Supply Systems Command
(NAVSUPSYSCOM or NAVSUP). The NAVICP is
located in two sites. They are the NAVICP Philadelphia
site (formerly known as Aviation Supply Office [ASO])
and NAVICP Mechanicsburg site (formerly known as
Ships Parts Control Center [SPCC]).
The primary function of the inventory manager
(IM) is to get and distribute material to effectively
support Navy activities. The IM provides support for
the life cycle of weapons systems and equipment
assigned by the HSC. After the material requirement is
determined, the IM locates the material in places that
ensures the quickest response time. The Navys
distribution system is involved with three stocking
levels. They are the consumer (including shipboard),
intermediate (ashore and afloat), and wholesale. The
distribution system is designed to push material to
wholesale stock points based on its customers
anticipated requirements. Ships and other customers
then pull or requisition material from the wholesale
stock points. When this pull of material is reported to
the IM, the IM replaces the item with push material to
the stock points. In cases where the wholesale stock
points also carry intermediate stock, the items are
pulled from the wholesale to satisfy retail requirements.
Items in stock are managed as wholesale or retail
material. Both involve a central IM at the NAVICP who
initially brings the item into the supply system. The
difference between wholesale and retail is the handling
of the item after it is brought in to the supply system.
Wholesale material is always under central
management at the NAVICP level. The IM positions
the material at stock points but retains management
responsibility. On the other hand, retail stock is locally
managed at the stock points, The local managers set the
level of inventory to satisfy local demands. Retail items
are replenished by using the demand, insurance, and
lead-time criteria.
5-1
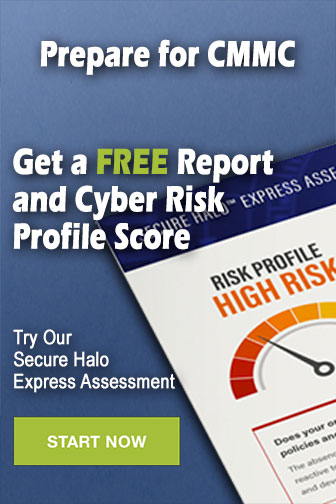