other approved closures.
You can use clean,
polyethylene bags if you do not have the approved
metal closures, providing the bags are adequately
secured and are protected from physical damage and
the entrance of water. When equipment is not being
used, store it in clean, dry areas. Minimize exposure
of in-service equipment to precipitation, wind-driven
sand, or other environmental contaminants.
Operational Use
Operate test stands equipped with hydraulic
manifolds for self-recirculation cleaning before they
are connected to equipment or components under test.
Recirculation clean the test stand for a sufficient
period of time to let a minimum of one pass of its total
reservoir contents through the internal filtration.
Closely monitor differential pressure of loaded filter
indicators during all SE operations after the fluid
reaches normal operating temperature (+85°F
minimum). Equipment operation is terminated
immediately upon appearance of loaded filter
indications. Replace the loaded element. You should
stop using the SE if the reservoir or outlet fluid is, or
is suspected to be, unacceptably contaminated.
Inform the supporting maintenance activity
immediately so that required remedial action can be
taken.
Periodic Maintenance
Supporting activities for hydraulic SE perform
periodic maintenance at prescribed intervals, unless
otherwise directed. At this time, samples are taken
from all hydraulic SE reservoirs (preferably at a low
point drain) and analyzed for particulate level and
water content.
If the fluid is unacceptable, it is
recirculation cleaned, purified, flushed, or purged.
Hydraulic filter elements that can be cleaned are
ultrasonically cleaned or replaced at the prescribed
maintenance interval.
Because of their large
dirt-holding capacity, disposable 3-micron pressure
line filters are replaced only upon actuation of their
differential pressure indicators. Disposable filters
that do not have differential pressure indicators are
replaced at the prescribed interval.
Age-controlled, deteriorative hoses used to carry
hydraulic fluid in SE units are not to remain in service
for more than 7 years beyond the manufacturers cure
date. Additionally, hoses of this type that are
internally located in the equipment are replaced at
each prescribed major rework interval, not to exceed
4 years. The date of the required removal and serial
number of the equipment is etched or peened on the
hose collar. Replace external deteriorative hoses used
to transfer fluid between SE and aircraft or
components under test that cannot be positively
identified as having been in use for less than 2 years
as soon as possible, and at regular intervals thereafter,
not to exceed 2 years. The date of required
replacement and the SE serial number is etched or
peened on the hose collars. Hoses should remain
attached to the equipment until replacement is
required. Upon completion of periodic maintenance,
hydraulic SE is certified as having a fluid
contamination level not in excess of Navy Standard
Class 3.
FLUID SAMPLING, ANALYSIS, AND
DECONTAMINATION
Fluid sampling points and procedures vary with
the SE type and model. For specific procedures
applicable to the particular equipment, you should
refer to NAVAIR 01-1A-17. Run the SE for a
minimum of 5 minutes before you take a sample.
This results in fluid flow through SE reservoirs,
which ensures a uniform distribution of contaminants.
On some SE models, you need to return the pressure
outlet to the reservoir fill opening to achieve such a
flow. Find and gain access to the reservoir drain
valve and other sampling points or adapters. You
need to remove dirt and other visible contaminants
from the exposed part of the drain valve and/or
sampling adapter. When taking a sample for a patch
or particle patch test, wipe the valve or adapter with a
clean, disposable cloth. Then, use the plastic wash
bottle in the Contamination Analysis Kit 571414 to
flush the fittings with clean trichlorotrifluoroethane
solvent (MIL-C-81302), 1,1,1-trichloroethane solvent
(MIL-T-81533), or dry-cleaning solvent (P-D-680).
When you have finished flushing the fittings,
open the reservoir drain valve and allow
approximately 1 quart of fluid to drain into a waste
receptacle. Without interrupting the flow of fluid,
take the required sample by letting an additional 4
ounces of fluid flow into a known clean sample bottle
(provided with the contamination analysis kit). Close
the drain valve after you remove the sample bottle
from the fluid stream. Label the bottle to indicate
where you took the sample. Repeat the sample-taking
procedure at other specified or available sampling
points, collecting each sample in a separate bottle.
Visually inspect the fluid collected in the waste
4-39
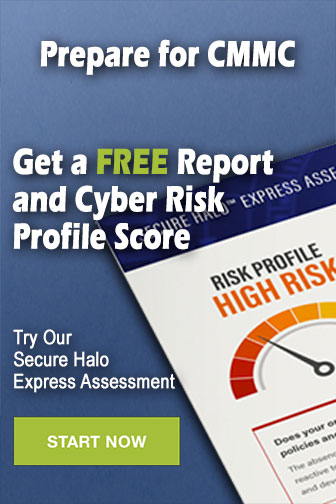