receptacle for free water. If free water is seen,
decontaminate the system according to applicable
procedures.
Contamination Analysis
Normally, contamination analysis of SE fluid
samples is accomplished by using the contamination
analysis kit.
You may use other approved
measurement methods, if available or if required.
Decontamination of unacceptable equipments is
performed by recirculation cleaning, purifying,
flushing, or purging, as required; these actions are
performed by the supporting activity.
Recirculation Cleaning
Recirculation cleaning is used when equipment is
unacceptably contaminated with particulate matter (in
excess of Navy Standard Class 3), but the fluid is
otherwise considered satisfactory. In recirculation
cleaning, the equipment is self-cleaned using its
internal filters, the 3-micron elements in particular.
You begin by operating the contaminated SE so
maximum circulation of fluid through the equipment
reservoir and internal 3-micron filters occurs.
Maintain the flow long enough to allow a total flow
equivalent to at least five times the total fluid capacity
of the equipment reservoir.
Monitor all filter
differential-pressure indicators throughout the
operation. If elements appear to be loaded, check and
replace them.
You should resample and analyze the fluid from
the reservoir.
If improvement is shown, but the
contamination level is still excessive, repeat the
process. If there is still no improvement, try to find
the internal contamination source, such as a failed
component. Replace any components you determine
to be contaminating the fluid, and continue
decontamination by draining, flushing, and refilling
the equipment with new filtered fluid. Recirculation
clean and resample, as before, to determine
acceptability. When you find the fluid samples from
the reservoir to be within acceptable limits,
recirculation cleaning may be terminated.
Flushing
Flushing is used to decontaminate SE heavily
contaminated with particulate matter, or when the
fluid contains a substance not readily removed by the
internal filters. To begin the flushing procedure, you
drain, flush, and reservice the equipment reservoir
using new filtered fluid. If contamination originated
at the pump, drain and flush the hoses and lines
directly associated with the pump output separately.
Operate the equipment so fluid flows through all
circuits. Allow output (or return line) fluid to dump
overboard into a waste receptacle. Continue flushing
until a quantity of fluid equal to the equipment
reservoir capacity has passed through the unit.
Closely monitor the reservoir level during the
operation, adding new filtered fluid, as required. This
prevents the reservoir level from dropping below the
one-third full point,
Take a sample and analyze the output and the
reservoir fluids. If the contamination level shows
improvement but is still unacceptable, repeat the
flushing operation.
If extensive flushing fails to
decontaminate the equipment, you should request
assistance from the supporting engineering activity.
Upon successful completion of system flushing,
recirculation clean the equipment for a minimum
period. Then, take a sample from the system to verify
the contamination level as being acceptable. When
you have done this, service the reservoir.
Purging
Purging of SE hydraulic systems is performed
only upon recommendation from, and under the direct
supervision of, the cognizant engineering activity. It
is the responsibility of the cognizant engineering
activity to select the required cleaning agents, provide
detailed cleaning procedures, and perform tests upon
completion of purging to ensure satisfactory removal
of all cleaning agents. Whenever possible, purging
operations are to be accomplished at a naval aviation
depot facility (NADEP). Intermediate maintenance
activities are not authorized to perform system
purging without direct depot supervision.
4-40
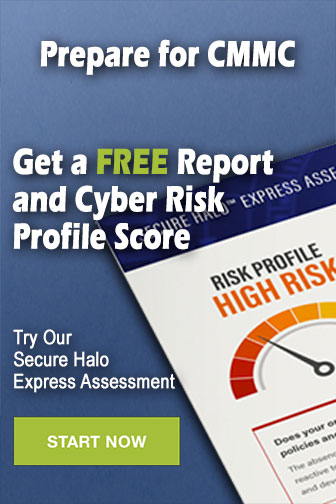