it to warm up with the controls set for bypass fluid
flow. Adjust the flow rate and operating pressures to
the required values using the volume and pump
compensator controls. Set the emergency relief valve
(if so equipped) to the operating pressure, plus 10
percent. The bypass control should be fully closed
during aircraft operation. Adjust the operating
pressure using the pump compensator control only.
The test stand is now ready to power the aircraft
hydraulic system.
NOTE: Use the procedures found in the
applicable MIM to actually power the aircraft
hydraulic system.
OPERATIONAL CHECKS. When operating
the test stand, you need to periodically check the
condition of system fluid through the sight glass. If
you see evidence of air, bleed the system at both the
test stand and air bleed points in the aircraft until the
fluid appears clear. Also, you need to monitor the
filter differential pressure indicators, particularly
those associated with the 3-micron filter assemblies.
In some cases, loaded filter indicators may extend due
to cold starting conditions. Reset the indicator and
continue to monitor it until the equipment reaches the
normal operating temperature. If a loaded filter is
indicated, shut down the equipment and return it to
the supporting activity. Another condition that would
require you to return the equipment to the supporting
activity is if the fault indicators light; in this case, shut
down the unit and return it to the supporting activity.
In case of an emergency (for example, a ruptured
hydraulic hose in aircraft), you should open the
bypass valve to relieve pressure and stop the flow of
hydraulic fluid to the aircraft. Pay attention to
warning signs such as a sudden drop in engine oil
pressure or any unusual engine noise. If any engine
part fails, Stop the engine immediately.
SHUTDOWN PROCEDURE.In aircraft
equipped with pressurized reservoirs, hydraulic
accumulators, or surge dampers, a reverse flow of
fluid through the aircraft filters could damage the
system. You need to use the correct shutdown
procedures. When you have finished the required
aircraft tests, leave the bypass valve in the closed
position. Reduce the volume setting to zero and
adjust the pressure compensator to minimum. Allow
several minutes for stored pressure in the aircraft to
bleed off, via normal internal leakage. On stands
equipped with a pressure and return line shutoff valve,
close the valve instead of reducing the volume and
pressure compensator.
Slowly open the pressure bypass valve. Let the
engine run at 1,000 rpm for about 5 minutes
(engine-driven models only), then push the throttle
down completely. Place the panel light switch in the
OFF position. Remove the external hoses from the
aircraft hose ports. Connect one end to the hose
storage manifold diconnects on the test stand. Do
not drag the hose ends on the deck or expose them to
contamination. Install all dust caps and plugs,
including those at the aircraft quick disconnects.
Close all the access doors to protect instruments and
controls.
MULTISYSTEM OPERATION.When per-
forming troubleshooting, rigging, and specific tests
on dual flight control systems that have tandem
actuators, you often need to apply SE hydraulic
pressure to two or three systems in an aircraft at the
same time. Simultaneous, multisystem operation
involves using separate hydraulic test stands for each
system, or by manifolding two or more systems to a
common test stand that has a sufficient flow
capability. Less equipment is needed with the latter
method, but it has several limitations that you should
know.
If you use a single test stand and manifold,
hydraulic fluid between the connected systems is
exchanged. If the fluid in one system is contaminated
with particulate matter smaller than 3 microns,
cross-contamination of the other system(s) will occur.
Using a single test stand may not satisfy differing
flow and back pressure requirements of the multiple
systems to be powered. Depleting or overfilling
aircraft reservoirs might result. If a single test stand
is used, high transient flow demands in one system
could adversely affect the performance of the other
systems. Total isolation between systems could
possibly degrade critical flight control system
performance tests. The use of jury-rigged manifolds
not specifically engineered for the purpose is a safety
hazard to personnel and a possible source of system
contamination.
Properly
designed
hydraulic
manifolds can be used in limited, specific applications
to power multiple hydraulic systems to form a
common hydraulic test stand. This configuration
must be evaluated by the cognizant engineering
activity to make sure it is acceptable and that its use is
strictly limited to that particular application. All
approved manifold use must be directed in the
applicable aircraft MIM, and complete information on
4-35
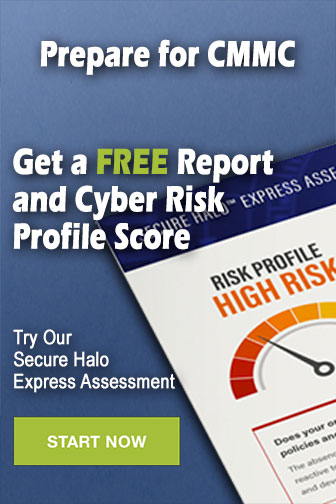