the major part of the electrical system components
from the hydraulic system.
Hydraulic System
The hydraulic system has two componentsa
reservoir, which supplies fluid through a helical,
screw-type boost pump and a filter to a variable
volume, pressure-compensated, axial piston,
high-pressure pump. Also, the hydraulic system has
three circuits-the dynamic test circuit, the static test
circuit, and the pump test circuit.
DYNAMIC TEST CIRCUIT.The dynamic
test circuit is used to test double-acting hydraulic
cylinders and other components requiring combined
pressure and flow.
STATIC TEST CIRCUIT.The static test
circuit is included in the hydraulic system. It is
essentially a compressed-air operated, low-displace-
ment, high-pressure pump that supplies fluid for static
pressure tests.
This circuit may be operated
independently of the other two test circuits. A safety
interlock prevents operation of this circuit when the
door of the test chamber is open.
PUMP TEST CIRCUIT.The pump test circuit
supplies controlled pressure and flow to a
variable-displacement, reversible-rotation, hydraulic
motor that, in turn, supplies power for driving
hydraulic pumps during tests,
Pneumatic System
The pneumatic system is composed of two
circuits. One circuit provides control, indication, and
filtration of externally supplied compressed air for the
operation of the hydraulic fluid temperature control
system, the hydraulic static pressure pump, and the
pneumatic static pressure booster. The second circuit
consists of a portable, compressed nitrogen cylinder
that supplies gas to a supply port through a manually
adjusted pressure regulator for static pneumatic
testing. A safety interlock prevents operation of this
circuit when the door of the test chamber is open.
Electrical System
Externally supplied electrical power is controlled
by a system located on the right-hand control panel.
The test stand START switch, pump ON/OFF
switches, and a test stand STOP switch are located
along the lower portion of this panel. There is also a
test stand STOP switch on the top left side on the front
of the test stand.
AIR BLEEDING
Air bleeding is a service operation. In this
operation, entrapped air is allowed to escape from a
closed hydraulic system.
For specific air bleed
procedures for each model aircraft, you should refer
to the applicable MIM. Excessive amounts of free or
entrained air in an operating hydraulic system results
in degraded performance, chemical deterioration of
fluid, and premature failure of components.
Therefore, when a component is replaced or a
hydraulic system is opened for repairs, the hydraulic
system must be bled of air to the maximum extent
possible upon repair completion.
Hydraulic fluid can hold large amounts of air in
solution. Fluid, as received, may contain dissolved
air or gasses equivalent to 6.5 percent by volume,
which may rise to as high as 10 percent after
pumping. Dissolved air generates no problem in
hydraulic systems so long as it stays dissolved, but
when it comes out of solution (as extremely minute
bubbles), it becomes entrained or free air. Free air
could enter a system during component installation,
filter element installation, or opening the system
during repairs.
Free air is harmful to hydraulic system
performance. The compressibility of air acts as a soft
spring in series with the stiff spring of the oil column
in actuators or tubing, resulting in degraded response.
Also, because free air can enter fluid at a very high
rate, the rapid collapse of bubbles may generate
extremely high local fluid velocities that can be
converted into impact pressures.
This is the
phenomenon known as cavitation. Cavitation causes
pump pistons and slide valve metering lands to wear
rapidly, commonly causing component failure.
Any maintenance operation that involves
breaking into the hydraulic system introduces air into
the system. The amount of such air can be minimized
by prebilling replacement components with new,
filtered hydraulic fluid.
Because some residual air
may still be introduced, all maintenance of this type is
followed by a thorough air bleed of the system. Most
hydraulic systems in high-performance aircraft are of
the closed, airless type; they are designed to
self-scavenge free air back to the system reservoir.
Air bleed valves
remove this air.
are provided at the reservoir to
Because free air resulting from
4-37
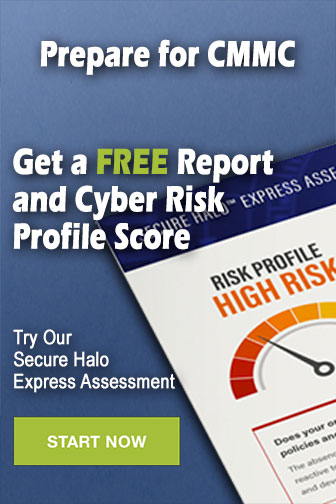