maintenance actions or other causes may enter the
system at a point remote from the system reservoir,
the system should be extensively cycled with full
power to transfer air to the reservoir, where it can be
bled off.
Air bleed valves are sometimes found at high
points in the aircraft circulatory system, filter
assemblies, and remote system components such as
actuators. These valves make the removal of free air
easier. Refer to the applicable MIMs for the location
and use of additional bleed points. In systems not
equipped with additional bleed points, you may have
to loosen line connections temporarily at strategic
points in the system, which permits removal of
entrapped air from remote or dead-end points. When
you bleed a system in this manner, be careful to avoid
excessive loss of hydraulic fluid, and prevent the
induction of air or contaminants into the system.
In many cases, air inspection procedures are
inadequate. SE specifically designed to detect and
measure air is not presently available in the fleet. You
should use indirect methods to determine the amount
of air present in a system. Operating the air bleed
valve on the reservoir reveals whether or not there is
air present in the reservoir. Large amounts of air
might be present somewhere else in the system and go
undetected. An effective means for measuring the air
in your system is known as the reservoir sink check.
In this method, the fluid level in the aircraft reservoir
is checked with the system, both pressurized and
nonpressurized.
The presence of air or any
compressible gas in the system causes the pressurized
reading to be lower (reservoir sink), indicating the
need for possible maintenance action (fig. 4-17). This
check is particularly effective when performed after a
long aircraft down period, in which case dissolved air
has had lots of time to come out of solution.
All air bleed operations must be followed by a
check of the system hydraulic fluid level. Fluid
replenishment may be required, depending upon the
amount of air and fluid purged from the system.
CONTAMINATION CONTROL
The direct connection between hydraulic SE and
the systems or components being checked or serviced
is necessary to minimize the introduction of external
contaminants.
Test units that are not properly
configured, maintained, or used may severely
contaminate hydraulic systems in operational aircraft.
It is your responsibility to make sure that hydraulic
SE is maintained and used according to existing
contamination controI requirements.
Configuration
SE used to service or test aircraft hydraulic
systems or components are equipped with adequate
output filtration having a rating of 3-microns
(absolute).
The 3-micron filter assembly is a
nonbypass variety, preferably equipped with a
differential pressure indicator. It is installed
immediately upstream of the major fluid discharge
ports.
Portable hydraulic test stands are equipped with
recirculation cleaning manifolds and fluid sample
valves for self-cleaning and fluid analysis before they
are connected to equipment under test.
Cleanliness
Hydraulic SE is maintained in a clean state. All
hydraulic SE is maintained as clean as practicable,
consistent with its construction and use. Always keep
external fluid connections, fittings, and openings
clean and free of contamination. When not in use,
protect fittings or hose ends using metal dust caps or
Figure 4-17.Reservoir level changes (reservoir sink)
presence of air in system.
4-38
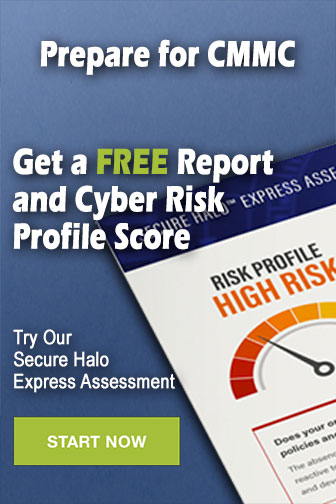