Figure 15-19.Basic penetrant process.
inspecting rods, tubes, cylinders, or wire. With the
encircling or inside coils, the entire circumference of the
specimen is evaluated at one time. Consequently, the
exact location of defects cannot be defined. The surface
coil has the ability to better define the exact location of
discontinuities.
Dye Penetrant Inspection
The dye penetrant inspection is a simple,
inexpensive, and reliable nondestructive inspection
method for detecting discontinuities that are open to the
surface of the item to be inspected. It can be used on
metals and other nonporous materials that are not
attacked by penetrant materials. With the proper
technique, it will detect a wide variety of discontinuities,
ranging in size from those readily visible down to
microscopic level, as long as the discontinuities are open
to the surface and are sufficiently free of foreign
material. Figure 15-19 shows the basic principles of the
penetrant inspection process. A penetrating liquid,
which contains dyes, is applied to the surface of a clean
part to be inspected. The penetrant is allowed to remain
on the surface of the part for a period of time to permit
it to enter and fill any openings or discontinuities. After
a suitable dwell period, the penetrant is removed from
the parts surface. You must exercise care to prevent
removal of the penetrant that is contained in the
discontinuities. A material called developer is then
applied. The developer aids in drawing any trapped
penetrant from the discontinuities and improves the
visibility of any indications. For more information
concerning the dye penetrant inspection, consult the
Nondestructive Inspection Methods Manual, NAVAIR
01-lA-16.
WELDING
Learning Objective: Recognize the qualifi-
cations and recertification process to become
a certified welder.
Welding is the most practical of the many metal
joining processes available to aircraft manufacturers.
The welded joint offers rigidity, simplicity, low weight,
high strength, and low-cost production equipment.
Consequently, welding has been universally adopted in
the building of all types of aircraft. Many structural
parts, as well as nonstructural parts, are joined by some
form of welding, and the repair of these many parts is
an indispensable part of aircraft maintenance.
QUALIFICATIONS OF WELDERS
For advancement, you should be familiar with the
operation of welding equipment and materials. You
should also be able to perform simple welding, brazing,
soldering, and cutting operations on ferrous and
nonferrous metals.
To weld on aircraft structural parts, you must be a
certified welder. To be certified as an aircraft welder,
you must pass a qualification test conducted in the
presence of a Navy inspector. Passing this test entitles
you to a certificate signed by the inspector attesting that
you are capable of welding the class of material and type
of weld indicated on the certificate.
Naval aviation depots have training programs for
the benefit of those desiring to qualify as aircraft
welders, and they have facilities for testing.
15-13
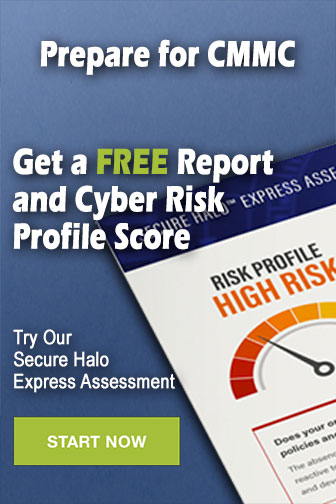