safety, economy, functional compatibility, and
convenience.
Arrangement
The arrangement of the furnishings should be
made on the basis of use rather that appearance.
Moving shop-installed equipment into an
out-of-the-way corner may improve the appearance of
the space but greatly reduces the efficiency of the
personnel using the equipment. It may also create a
safety hazard. A good rule to follow is to locate the
equipment where it can be safely used by the greatest
number of authorized persons with minimum effort in
the least amount of time.
Work tables and benches should be positioned
with respect to fixed equipment so that the equipment
most often used is most quickly and easily reached.
Electrical and compressed air outlets should be readily
available to workbenches. Needless delays are caused
by having to rig unnecessarily long connections from
poorly located outlets.
You should give special considerations to the
installation of special lighting, such as explosionproof,
vaporproof, or interference-free lights, near
workbenches where specific or intricate work is to be
performed. Another special consideration is that of
ventilation. All work spaces should have adequate
ventilation under all conditions that are expected to
exist in that work space.
The use of paint in various colors to emphasize
portions of intricate machinery for safety and
reflective purposes is known as dynamic painting.
Painting in this category should be kept in an efficient
state for maximum effectiveness; however, this type
of paint should not be used for normal building
maintenance.
The work center layout plan should have a
provision for an information or bulletin board. Safety
posters, maintenance posters, instructions, notices,
plan of the day (POD), and such other information as
appropriate should be placed on this board. This board
should be located in a prominent place in the work
center, preferably near the entrance where everyone
assigned must pass at sometime during the day.
Material on the bulletin board should be kept current,
expired notices removed promptly, the current POD
posted early, and safety posters rotated periodically. If
the same material is presented in the same format day
after day, personnel begin to ignore the board. A new
arrangement will arouse curiosity and interest.
Scheduling and Assignment of
Workload
Your most important concern as a supervisor is the
assignment and accomplishment of the scheduled and
unscheduled workload.
Scheduled maintenance can be defined as
maintenance that is required by hours, calendar
periods (days or weeks), and starts. This type of
maintenance is always anticipated and planned. By
tracking flight or operating hours, maintenance control
knows exactly when a particular aircraft is due for a
phase inspection. It is also easy to determine when an
aircraft or piece of equipment is due for a 28-day
inspection.
Unscheduled maintenance is defined as
maintenance that occurs on aircraft or equipment other
than scheduled. For example, an aircraft develops a
hydraulic fluid leak on preflight, or perhaps while
performing scheduled maintenance on an aircraft
engine, a worker discovers a cracked or chaffed line.
The repair or replacement of that line is unscheduled
maintenance.
As the work center supervisor, you should attempt
to coordinate the installation of technical directives
(TDs) and correct minor discrepancies to coincide
with scheduled maintenance. You may not be
authorized to wait until the next scheduled
maintenance period for the installation of a TD; the
assigned category (priority) determines the maximum
allowable time period for compliance with the
directive. A directive classified IMMEDIATE
ACTION may be issued with instructions to be
completed "prior to further use of equipment" or "prior
to next flight"; a directive classified ROUTINE
ACTION must be accomplished within 18 months of
the date of issue.
The supervisors objective is the satisfactory
completion of assigned tasks in a reasonable amount
of time, using available personnel and materials as
efficiently as possible. To achieve this objective, the
supervisor must become skilled in estimating the
amount of time required for each task and the number
ofworkers required. To be able to estimate effectively,
you, as the supervisor, must be familiar with the task
and know the capabilities of your personnel. You must
realize the importance of assigning qualified and
unqualified persons to the same job, when possible.
Allow for planned interruptions, and yet do not operate
on so tight a schedule that minor, unplanned
6-4
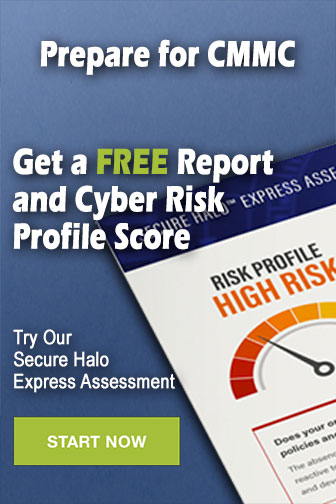