interruptions completely disrupt the maintenance
effort.
Q7. Describe scheduled and unscheduled
maintenance.
Estimating Time and Personnel
Requirements
Estimating times for completion of maintenance
tasks will be one of the supervisors responsibilities.
The quality and quantity of personnel assigned to
perform these tasks directly affect the time required
for completion. Other items that affect time are the
type and complexity of maintenance, the availability
and condition of materials, work center tools and
equipment, and working conditions or job site
(in-shop, cold flight deck, etc.).
Probably the most important single aid in
estimating time and personnel requirements for
maintenance tasks is a JOB PLAN. Within an office,
a work center, or on the line, job planning is one of the
most important functions of the supervisor. The person
who allows an organization to run haphazardly, who
never thinks ahead, who is never ready for an
emergency or extra workload, and who does not
delegate work or trust subordinates is not a good
supervisor.
6-5
Proper planning saves time, reduces cost, and
makes the work easier, safer, and more pleasant for
everyone. Proper planning can eliminate friction and
confusion, as well as make better use of in-port periods
for tasks that cannot be performed underway; it also
frees the supervisor from petty details. Planning
expedites the work, eliminates "bottlenecks," and
makes the supervisor's job easier.
The following hints can help you as a supervisor.
In planning a job, use the BIG SIXWHAT, WHY,
WHERE, HOW, WHO, and WHEN.
1. WHAT is the task? What does it involve and
what special tools may be required?
2. WHY is the work to be done? (This helps to
establish priorities.)
3. WHERE can the job be done? (In-shop, hanger
bay, etc.)
4. HOW is the job done? (Electrical or air
requirements, etc.)
5. WHO is affected? (Are there other work centers
involved? Who is the best qualified?)
6. WHEN is the job to be started and what are the
time constraints?
It is not necessary to have an answer to all of these
questions; however, the more you can answer, the
better plan you will have. As supervisor, start each new
shift by checking over the work to be done; plan for
maximum use of manpower, equipment, and material.
Also, ensure that you attend the maintenance meeting
with other work center supervisors. Periodically
during the shift, make checks to ensure that work is
progressing as planned.
Daily Maintenance Meeting
The daily maintenance meeting is one of the best
tools for ensuring a smooth flow of information about
maintenance between shifts and other supervisors.
This meeting allows all the supervisors within your
department or division to brief the maintenance chief
on the status of equipment, components, or aircraft that
currently have ongoing work or are scheduled to have
maintenance performed. It also allows supervisors to
coordinate time frames for sharing certain facilities,
equipment, or electrical power requirements. In
addition, these maintenance meetings may bring to the
attention of the maintenance chief items of material
that may be difficult to obtain. It may identify certain
document numbers that require "hand massaging" by
the supply chief.
Q8. What is the most effective tool for ensuring a
smooth flow of information regarding
maintenance between shifts, other work centers,
and maintenance control?
Personnel Work Assignments
Rotate work assignments so that each person in
you work center can develop skills in all phases of
maintenance. Personnel in lower paygrades should be
encouraged to get involved in many different types of
maintenance. A worker who understands a system or
aircraft will be a better troubleshooter. Additionally,
when you rotate work assignments and encourage a
wide range of maintenance skills, the work becomes
more interesting to the worker. More interest, more
quality! If one highly skilled mechanic performs all of
the work of a certain type, the supervisor and the work
center would suffer if that technician were to transfer,
be assigned TAD, or even take a period of well earned
leave; this is another reason for rotating work
assignments. Assign less experienced workers to work
with the skilled mechanics so they can become
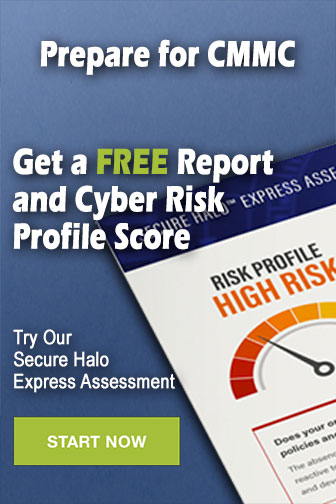