proficient at a particular skill. This also permits each
person to broaden his/her knowledge.
Allowing for Planned
Interruptions
During an average workday, personnel will need
to leave their work center for various personal reasons;
this may easily interrupt the scheduled workload.
Some reasons can be anticipated and some cannot.
Among those that can be anticipated are training
lectures, inspections, immunization schedules, rating
examinations, meals, watches, and other military
duties.
Before assigning a task, the supervisor should
determine what delays can be anticipated. It may be
possible to arrange assignments so that work
interruptions are held to a minimum. It is much easier
for the same technician to complete a task that he
started than for another to pick up where the first
worker left off. If interruptions cannot be avoided, the
supervisor should allow for these predictable delays
when estimating completion times.
QUALITY ASSURANCE
LEARNING OBJECTIVE: State the purpose
and concept of Quality Assurance.
When you progress up the ladder of responsibility
in aviation maintenance, you become more involved
in quality assurance (QA). You may be assigned as a
QA representative or a collateral duty inspector.
Therefore, you must become quality conscious.
The quality assurance (QA) division determines
deficiencies, analyzes discrepancy trends, prescribes
inspection procedures, and determines the quality of
maintenance accomplished. The division also
provides follow-up action and functional guidance to
stimulate QA at the departmental level.
NOTE: At the time of publication of this training
manual, the NAMP Policy Committee has determined
that Naval Aviation Maintenance Program Standard
Operating Procedures (NAMPSOP) will take the place
of Maintenance Instructions (MIs) throughout naval
aviation. MIs are mentioned frequently throughout
this chapter as they are still referred to in the NAMP.
The next update of the NAMP may reflect the use of
NAMPSOP rather than local MIs. Refer to OPNAV
NOTICE 4790 for further information regarding
NAMPSOP.
CONCEPTS OF QUALITY
ASSURANCE
The QA concept is fundamentally the prevention
of the occurrence of defects. This includes all events
from the start of maintenance operations until their
completion. Quality is the responsibility of all
maintenance personnel. Achievement of quality
assurance depends on prevention, knowledge and
special skills.
Prevention of the occurrence of defects relies on
the principle of eliminating maintenance failures
before they happen. This principle extends to safety of
personnel, maintenance of equipment, and virtually
every aspect of the total maintenance effort.
Prevention is concerned with regulating events rather
than being regulated by them.
Knowledge is obtained from factual information.
This knowledge is acquired through the proper use of
data collection and analysis programs. The
maintenance data collection system provides
maintenance managers limitless quantities of factual
information. Correct use of this information gives
management the knowledge needed to achieve
maximum readiness of aircraft and weapons systems.
Special skills, normally not possessed by
production personnel, are required by a staff oftrained
personnel for the analysis of data and supervision of
QA.
The terms inspection, quality assurance, and audit
(as used in this context) have distinct meanings and
should be used accordingly. The following definitions
are provided to clarify the differences in these terms.
Inspection is the examination (including testing)
of supplies and services, including raw material,
documents, data, components, and assemblies.
Inspection is done to determine if the supplies and
services conform to technical requirements.
Quality assurance is a planned and systematic
pattern of actions necessary to provide confidence that
the product will perform satisfactorily in service. QA
is also the monitoring/analyzing of data to verify the
validity of these actions.
An audit (as it applies to QA) is a periodic or
special evaluation of details, plans, policies,
procedures, products, directives, and records.
QA provides an efficient method for gathering,
analyzing and maintaining information on the quality
characteristics of products, on the source and nature of
6-6
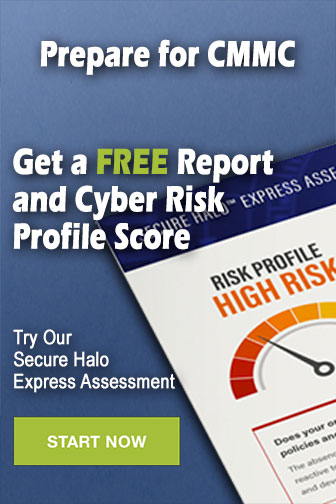