Figure 12-7.Converter installed in an aircraft.
allowed to go unchecked, pressure in excess of
12,000 psig could be generated. To prevent this
potentially hazardous situation, a relief valve is
incorporated. The relief valve is set to relieve
excess pressure in the converter assembly at
approximately 110 psig.
9. As a demand is placed on the converter
by the aircrewman, LOX is forced into the
buildup coil to replace consumed oxygen. As this
process is repeated, the LOX level in the converter
drops, increasing the void area at the top. As the
size of the void area increases, pressure decreases,
and is sensed by the bellows in the pressure closing
valve. When pressure falls below approximately
75 psig, the bellows expand, opening the valve.
With the valve open, pressure from the buildup
coil passes through the valve and into the top of
the converter. This pressure, coupled with the
pressure created by vaporizing LOX contained in
the converter, again builds to approximately 75
psig and closes the pressure closing valve. This
process is repeated as long as a demand is being
placed on the converter.
10. A heat exchanger is incorporated into the
aircraft tubing to further warm the gaseous
oxygen to a breathable temperature.
11. An additional relief valve, set at approx-
imately 115 psig, is installed in the aircraft
oxygen plumbing to provide additional protection
against overpressurization of the converter and
supply lines of the system.
PERFORMANCE TESTING
To be sure the converter is functioning, a series
of bench tests is made. These tests are made
using the test stand and the test stand calibration
correction cards, shown in figure 11-6 in chapter
11 of this manual.
12-21
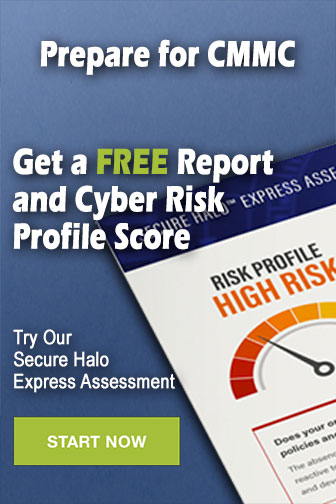