TD Routing and Tracking Sheet (Part 1)
1. CTP Librarian Action:
a.
b.
2. QA
a.
b.
c.
d.
Stamp and date original TD and maintain as master.
Stamp and date copy and route to QA for screening.
CTP Librarian Signature:
Action:
Date:
TD has been screened and applies/does not apply (circle one) to
Equipment:
TD compliance is required no later than:
Remarks:
Deliver this form and copy of TD to MMCO and brief Maintenance Chief on TD requirements.
Screening QARs Signature:
3. Maintenance/Production Control Action:
a.
Update NALCOMIS TD Configuration File.
b.
Initiate (to order parts/issue/no parts required) MAFs.
c.
Complete Columns I, II, and III of Part 2.
d.
Screen for Weight and Balance application (O-level only).
Weight & Balance Officer Signature:
Date:
e.
Initiate, as applicable to LRCAs, a TD Screening Request (I-level only).
Maintenance/Production Control Signature:
f.
Route Parts 1 and 2 to QA (O-level) or ICRL Manager (I-level).
g.
Add TD requirements to ICRL.
ICRL Program Manager Signature:
Date:
Date:
Date:
h.
Route Parts 1 and 2 to QA (I-level).
4. QA Action:
a.
Verify, MAF Copy 2 (or NALCOMIS hard copy notice) against Part 2.
b.
File Part 2 with all MAF Copy 4s (or NALCOMIS hard copy notices) issued.
c.
As signed off MAF Copy 4s are received, verify logs and records, weight and balance entries have been
made and initial columns IV, V and VI of Part 2.
d.
Data Analyst shall initial Column VII after reviewing MDR-4-1 or MDR-4-2 to ensure that the MAF
was processed.
e.
Discard Part 1.
AZf0304
Figure 3-4.TD routing and tracking sheet (part 1).
3-11
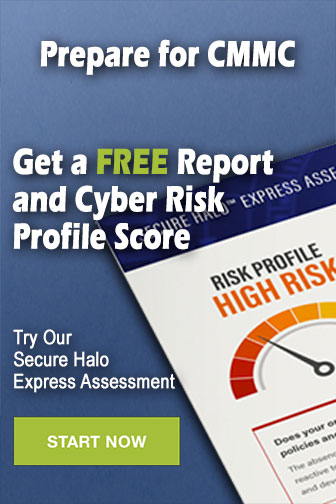