All copies of the five-part MAF contain the same
information. Copy 2 of the MAF is used for material
usage reporting. At the organizational maintenance
level, the five copies of the MAF are as follows:
Copy 1work center register and processing copy
Copy 2quality assurance suspense file copy
Copy 3maintenance control register
Copy 4aircraft discrepancy book copy
Copy 5work center daily audit copy
At the intermediate maintenance level, the five
copies of the MAF are used as follows:
Copy 1control and processing copy
Copy 2supply department register
Copy 3production control register
Copy 4component RFI/BCM copy
Copy 5work center register/daily audit copy
MAF Data Fields
NALCOMIS system-generated MAFs and
five-part MAFs are similar in appearance and content,
but operating procedures for each are different. MAF
data blocks and data fields apply to both
NALCOMIS-generated and five-part MAFs. Each data
field on the MAF serves a specific purpose. Most of the
information in these data fields is entered in coded
form. We will describe each data block or data field on
the MAF. Refer to figure 4-4.
ENTRIES REQUIRED SIGNATURE block.
Entries in this block ensure that historical records are
updated and that required actions are accomplished
before MAFs are forwarded to data services facilities
for processing. Maintenance control logs and records
personnel should screen all MAFs, check the
appropriate block or blocks, and enter their name and
rate in the signature portion of this block. This
signature certifies that the MAF has been screened and
that no further entries are required and that all
applicable logs and records entries have been made. For
OMA NALCOMIS users, this block is computer
generated.
LOCAL USE block. This block may be used as
desired.
REFERENCE block. This block contains the
supply reference data to assist material control in
requisitioning required material.
ACCUMULATED WORK HOURS block. This
block contains the name/shift, toolbox inventory, date,
man-hours, and elapsed maintenance time columns.
Name column. Contains the name and shift of
personnel who perform the work.
Tool box column. This column is used to help
ensure that tools are not left on the job. Each
worker who uses a tool container on a job
enters the number of the container in this
column. Upon return to the work center, the
work center supervisor or collateral duty
inspector (CDI) does a sight inventory of the
tool container and indicates a complete
inventory by initialing or stamping to the right
of the tool container number.
Date column. The Julian date on which the action
takes place.
Man HRS (hours) column. The number of
man-hours that were expended to correct the
discrepancy (in hours and tenths of hours).
Elapsed M/T (Maintenance Time). The number of
clock hours that were involved in making the
repair (in hours and tenths of hours). For
example, if three people worked together for
2.5 hours to make a repair, the total man-hours
would be 7.5, and the elapsed M/T would be
2.5 hours.
ACCUMULATED AWM HOURS block.
Contains a record of the hours that are accumulated
during the SCIR-related time of a discrepancy. Includes
the beginning date and time of the AWM period with
the proper reason code. The accumulated AWM hours
are entered in the hours section of this block.
NOTE: A complete list of AWM codes are
contained in an appendix to the NAMP.
H-Z FAILED/REQUIRED MATERIAL section.
The blocks in this section document the following
information:
A failed part occurs without an awaiting part
(AWP) situation
A failed part and an AWP situation occur
simultaneously (IMA only)
An AWP situation without a failed part occurs
(IMA only)
A supply request only, no failed part or AWP
situation
4-14
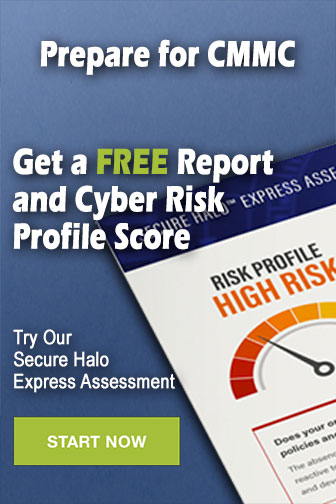