unless an earlier change is forced by one of the fol-
lowing conditions:
The pressure drop across either the filter or the
monitor elements reaches 20 psi.
The combined pressure drop across the filter and
monitor elements reaches 25 psi.
A significant drop in differential pressure occurs,
indicating an element rupture.
The differential pressure fails to increase after an
extended pied, indicating either ruptured elements or
improper installation.
The complete shutdown of fuel flow and/or a
very rapid increase in pressure differential across the
monitor elements. This usual] y indicates a failure of the
filter/separators. If this condition occurs, both the fil-
ter/separator and monitor elements must be changed.
During filter changes, the permanent second-
stage water separator elements should be tested for
their ability to repel water. If the separator element
does not repel or cause the water to bead, it should be
washed with warm water and tested again.
Records and Reports
Observation of abnormal operating conditions is
vital to a good preventive maintenance program. The
detection of small operating faults and their subsequent
minor correction or repair can often avert the develop-
ment of major problems requiring extensive repairs.
Such conditions must be promptly reported to the
proper authorities in order to achieve the necessary
repairs or corrections. These deficiency reports are in
written form.
Facilities must maintain maintenance records in
sufficient detail to provide the following:
Identification of each major structure, equip-
ment item, group of items, or system
Current maintenance status, including un-
funded deficiencies and uncompleted job or-
ders
Past maintenance history, including description
and cost of major repairs or replacements
Recommendations for future programmed re-
pairs or replacements, including estimates of
funds or manpower requirements
ASHORE OPERATING PROCEDURES
LEARNING OBJECTIVE: Explain the proce-
dures for various ashore fueling operations.
The operating procedures presented and dis-
cussed in this section are for general types of fuel
facilities and equipment common to all or most activi-
ties engaged in the fueling of aircraft. Since the actual
facilities and equipment vary greatly from installation
to installation, these procedures and accompanying
information are designed to serve as a basic outline
and guide. As always, use your stations specific op-
erational procedures for actual fueling and defueling
operations.
SPILL PREVENTION AND CONTROL
Proper training of fuel-servicing personnel is essen-
tial. Proper maintenance of the equipment is equally
essential. Leaking or malfunctioning equipment must
be removed from service. Self-closing nozzles or dead-
man controls must not be blocked open or bypassed.
Kinks and short loops in fuel hoses should be avoided.
In addition, a fuel-spill/fire prevention drill must be
conducted at least quarterly.
When a spill is observed, the fuel servicing must
be stopped immediately by release of the deadman
control, by closing the nozzle handle, or by operation
of the emergency fuel shutoff. The supervisor is noti-
fied at once, and the operation must not be resumed
until authorized by the supervisor. Every fuel spill
must be investigated to determine the cause, whether
emergency procedures were properly carried out, and
what corrective measures are required.
Priming Spills
Pint-size spills, involving an area less than 18
inches in any dimension, require no emergency action
during cold-refueling operations. However, ramp per-
sonnel should stand by with a fire extinguisher until
operations are complete and/or the aircraft departs.
A spill or leak of any size is cause for terminating a
hot-refueling operation.
Small Spills
Other small spills involving an area of from 18
inches to 10 feet in any dimension must have a fire
guard posted, equipped with at least one fire extin-
guisher. Either absorbent cleaning agent or emulsion
7-13
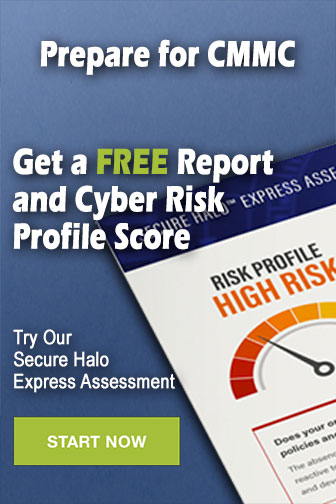