recirculated long enough to flush out all piping down-
stream of the fuel monitor elements.
17. Check the operation of the pump. Listen for
unusual sounds and feel for overheating and/or abnor-
mal vibrations.
18. Obtain a nozzle sample and visually inspect it
for color, water, and solids. Record the results.
19. With the system recirculating, observe and re-
cord the pressure drop across the filter/separator and the
monitor.
Weekly Checks
The weekly check is performed by a senior opera-
tor or fuel shop personnel. The weekly inspection is
also required to be performed on equipment being
returned to service following any DOWN time that
exceeds 72 hours. The typical weekly inspection
checklist is as follows:
1. Complete items 1 through 17 on the daily check-
list.
the CFD and FWD. Log the results in the appropriate
laboratory log.
3. Clean and inspect all nozzle screens (pressure
and overwing).
4. Inspect tires, brakes, horn, windshield wipers,
steering, trainer coupling and electrical wiring. The
brake linings and/or pads must be checked by normal
application of the brake while observing pedal travel.
Test the emergency brake under drive conditions. Make
sure all electrical wiring outside of the cab is encased in
tubing that terminates in securely mounted vapor-tight
fixtures or junction boxes with compression fittings.
The use of a transportation inspector is recommended
for these checks.
5. Measure and record the pressure drop across the
filter/separator and the fuel monitor using a sensitive,
hand-held pressure gage accurate to 1 psi, with gradu-
ations in 1 psi, or smaller, units, This measurement
MUST be taken with the system operating under normal
flow conditions.
Monthly Checks
The monthly checks require special equipment
and moving of mobile equipment to a location other
than the operating area. The typical monthly checklist
is as follows:
1. Complete the daily and weekly checklists.
2. Check the continuity of grounding cables, bond-
ing cables, and reels. Continuity must be measured with
the cable in the stowed, intermediate, and fully extended
positions. Check the continuity of the grounding cable
on each overwing fueling nozzle.
3. Inspect and clean all line strainers, including the
meter strainers when installed.
4. Test the anti-driveaway device installed on all
refuelers.
5. Perform the engine spark check at night. The
purpose of this check is to locate any electrical arcing
over the outside surfaces of wiring, spark plugs, and the
like. Any auxiliary engines should be included in the
test. Any observed arcinghowever slightis suffi-
cient cause to remove the equipment from service.
6. Test maximum flow rate. If pressure tests indi-
cate that nozzle pressure exceeds 55 psi or that the flow
rate exceeds 600 gpm, the equipment must be removed
from service.
7. Test the primary pressure-control system.
8. Check the refueling adapters (receptacles), us-
ing the go/no-go gage.
9. Make sure fuel-handling equipment is marked
in accordance with NAVFAC P-300 or MIL-STD-161.
Periodic Inspection and Annual Record
The Periodic Inspection and Annual Record pro-
vides an important historical record for each piece of
refueling equipment. It is a written record of inspec-
tions, calibrations, element changes, and other main-
tenance actions performed through the year. As with
other checklists, this record may be tailored to meet
the requirements of each station.
Filter/SeparatorFuel-Monitor
Pressure Log and Graph
The pressure drop across each housing must be
accurately determined so that the integrity of the ele-
ments can be verified. Over time, differential pressure
will increase as more and more dirt and/or water is
trapped. Additionally, ruptures or breaks are identi-
fied by a significant drop in differential pressure. All
activities must maintain a log for each filter or moni-
tor.
Filter and monitor elements in refueling equip-
ment or at truck-fill stands are changed every 3 years
7-12
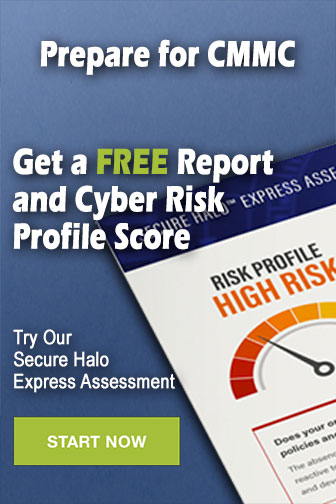