processing material transfer only if record balances are
suspect or the item is classified or sensitive.
SCHEDULED INVENTORY. This inventory
is accomplished at a given time for a specific material
category. The inventory frequency for each type of
material is discussed in the following paragraphs.
General Supplies. A random statistical sample
inventory of the total population of items in storage is
conducted quarterly to determine the overall inventory
accuracy rate. Activities under the Uniform Automated
Data Processing System-Stock Points (UADPS-SP) use
the Statistical Accuracy Techniques and Measurements
Analysis (STATMAN) system to perform the sample
inventory. The non-UADPS-SP activities have the
option to perform an annual wall-to-wall inventory
instead of a quarterly sample inventory.
For arms, ammunition, and controlled inventory
items, use the procedures described in OPNAVINST
5530.13. Sonobuoys must be inventoried annually.
Narcotics, drug abuse items and alcohol, and
precious metals (Security codes Q and R) are
inventoried quarterly.
Refer to NAVSUPINST
4440.146 for additional information.
Classified (Security codes A through H, K, L, O, S,
and T) items are inventoried annually as required by
DODINST4140.35, In addition to the annual inventory
requirement, NAVSUP Publication 1, Volume II,
Supply Ashore, requires the maintenance and
reconciliation of dual stock records. This is performed
by matching the manual stock records and the master
stock item record (MSIR). The manual stock record is
to be maintained on NAVSUP Form 766, Stuck Record
Card, by the storage branch/division. To ensure
inventory accuracy, the annual classified inventory and
the reconciliation of the manual stock record must be
scheduled alternately at six-month intervals.
Pilferable items (Security codes I, J, M, V, W, X, Y,
Z) must be inventoried annually as required by
DODINST4140.35.
Consumer Level Stock. These are items carried
in service marts (SERVMARTS), shop stores, ready
supply stores, and W purpose repairables that are part
of the fixed allowance assets.
Items in SERVMART must be inventoried once
each fiscal year according to NAVSUPINST 4400.59.
The inventory adjustments (based on dollar value of
gains or losses) must not exceed one percent of the total
sales since the last scheduled inventory. If the inventory
adjustment is over one percent, an inventory must be
taken quarterly until the financial adjustments are
within limits as prescribed by NAVSUPINST 4400.59.
The shop stores and ready supply stores are
inventoried once each fiscal year according to NAVSUP
Publication 1, Volume 2, Supply Ashore.
Inventory the fixed allowance assets in W purpose
(SHORCAL) annually according to NAVSUPINST
4440.160.
Scheduled Inventory Requirements
During the fourth quarter of each fiscal year, stock
points prepare a physical inventory schedule for the
following fiscal year. The stock points should consider
the following factors when preparing the schedule:
1. The estimated number of scheduled and
unscheduled inventories to be conducted for the fiscal
year.
2. Results of the recent statistical random sample
inventories and location surveys. If the results dictate
the need for a wall-to-wall inventory, the annual
schedule must be updated with the scheduled inventory
requirement.
3. Requests for inventory from the NAVICP/DSC.
4. Mandatory inventory requirements described in
previous paragraphs.
Format for Annual Physical Inventory
Schedule
The annual schedule indicates the inventories
projected for execution during each quarter of the fiscal
year. The schedule should be in the following format:
1. Inventory Segment. This column identifies the
type of material to be inventoried. Some examples of
the different types of material are classified, specific
supply group or class, and so forth.
2. Scheduled Inventory Line Items. This contains
the number of line items included in the segment of
inventory.
3. Warehouse/Warehouse Areas. This identifies
the warehouse or warehouse areas in which the
inventory is conducted.
4. Preliminary Cutoff Date. At start of business on
this date (7 to 15 days before the actual cutoff date),
inventory controls are established and tracking of
in-process transactions begin.
5-8
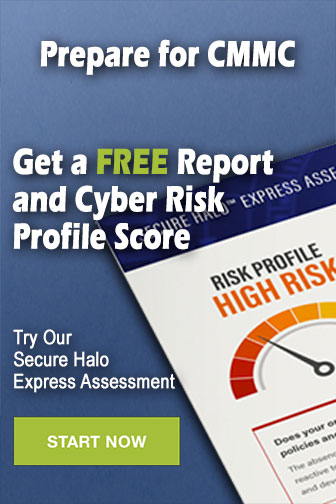