8. When purging is completed, turn the purge
unit power switch OFF, secure the N2 supply
cylinder valve and the purge unit inlet valves.
Disconnect the purge unit from the converter.
NOTE: Should the unit fail a test, the first
step of the repair action is to repurge the
unit.
INSULATION RESISTANCE TEST
(EMPTY)
To perform the insulation resistance test,
proceed as follows:
1. Secure the empty converter in the rack
provided on the test stand countertop.
2. Using the test stand cable assembly,
connect the upper terminals of the high
capacitance cable assembly to terminals A and B
of the liquid oxygen quantity gauge capacitance
type tester.
3. Turn the power switch ON and allow the
tester to warmup 10 minutes prior to proceeding.
4. Turn the MEGOHMMETER RANGE
SELECTOR to its X-1 position.
5. Turn the FUNCTION SELECTOR knob
to the A AND B position. Record the reading on
the meter in the space provided on the
Performance Test Sheet. Reading should not be
less than 2.0 megohms.
6. Turn the FUNCTION SELECTOR knob
to A TO GROUND and B TO GROUND
positions respectively. Record the readings in
spaces provided on the Performance Test Sheet.
Readings should not be less than 1.0 megohm in
either position.
7. If insulation resistance readings are less
than allowed, connect the cable assembly to the
lower probe terminals, and repeat steps 5 and 6.
8. If readings are acceptable, replace the high
capacitance cable with the low capacitance
assembly. Repeat steps 5 and 6. If readings are
acceptable, proceed to step 11.
9. If readings continue to be less than
acceptable, moisture may still be present in the
sphere assembly. Purge the converter and repeat
the test.
10. Converter assemblies that fail the insula-
tion resistance test, and cannot be corrected by
replacing the low or the high capacitance cable
assembly or by purging, are condemned.
11. Leave all connections unchanged and start
the capacitance test (empty).
CAPACITANCE TEST (EMPTY)
To perform the capacitance test, proceed as
follows:
1. Turn the CAPACITANCE RANGE
SELECTOR knob to the X-10 position.
2. Turn the FUNCTION SELECTOR knob
to its CAPACITANCE (UUF) position.
3. Record the meter reading in the space
provided on the Performance Test Sheet. Reading
should be 121.5 to 125.5 micro-microfarads
(UUF).
4. If this reading is not within these limits,
moisture may still be present in the sphere. Purge
converter again and repeat the capacitance test.
5. Converter assemblies that fail the
capacitance test and cannot be corrected by
purging are condemned.
6. Turn the power switch off and disconnect
the test stand cable assembly.
RELIEF VALVE TEST
To follow this description, you will find it
helpful to refer back to figure 11-4 of the test
stand in chapter 11. To perform the relief valve
test, proceed as follows:
1. Disconnect low and high capacitance cable
assemblies from lower probe terminals.
2. Disconnect the buildup tube assembly from
the buildup port of the fall, buildup and vent
valve, and from the pressure closing valve. Hold
the 45-degree elbows with open-end wrench to
prevent turning while loosening tube nut
connections.
3. Cap 45-degree elbow in buildup port of fill,
buildup and vent valve.
4. Using Test Stand Hose Assembly, P/N
59A120-B5-14, connect test stand BELL JAR
BOTTOM COUPLING C-1 to the 45-degree
elbow on converter pressure closing valve.
5. Using the Test Stand Hose Assembly P/N
59A120-B5-52, connect the converter quick-
disconnect coupling to the test stand FLOW-
METER CONNECTION, NIP-4.
6. Turn the FLOWMETER SELECTOR
valve V-1 to the 0-150 lpm position. Open the
TEST PRESSURE GAUGE-TO-BELL JAR
valve, V-2.
7. Open the OXYGEN SUPPLY valve, V-6,
slowly. Damage to test stand gauges could result
from rapid surges in pressure if this valve is
opened too rapidly. Pressure applied will be
indicated on TEST PRESSURE GAUGE, PG-1.
8. The relief valve relieves a minimum rate of
100 lpm, as indicated on the FLOWMETER
12-28
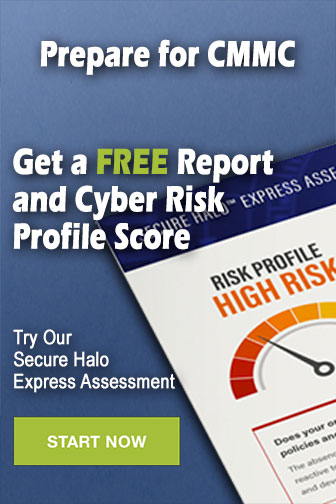