The fluid cooler body is a cylindrical steel shell
with two flanged ends. The body of the cooler has four
equally spaced holes in each end to provide a means of
draining and venting the cooler. These holes are
normally closed with pipe plugs or vent valves. One
end of the cooler has a cooler head assembly that forms
a cap for one end of the body and provides an inlet for
engine fluid coming from the accumulator. The cooler
head assembly is a disc-shaped steel casting with an
opening in the center, which is flanged to the fluid inlet
piping.
A copper annealed gasket is used as a seal between
the cooler head and the body to prevent fluid leakage.
The head is bolted to the body. The coolant (salt-water)
flows through a tube assembly that consists of 107
U-shaped copper tubes supported inside the cooler
body by three circular baffle plates. A tube head is
bolted to the end of the cooler, opposite of the cooler
head. A copper annealed gasket is used as a seal against
fluid leakage between the tube head and the cooler
body. Cooled fluid passes through the center of the tube
head, through piping, to the retract valve. Two
kidney-shaped manifolds (one inlet and one outlet
manifold for the coolant to flow) are bolted to the outer
face of the tube head.
Saltwater piping leading to and from the inlet and
outlet manifolds has shutoff valves, one intake and one
discharge, that are used to throttle the flow of salt water
and maintain the desired fluid temperature. Shutoff
valves are also provided in the fluid inlet and outlet
lines to provide a means of isolating the fluid cooler in
the event of cooler leakage, and a bypass valve is
provided to direct the fluid from the accumulator to the
retract valve when the cooler is isolated. To prevent
corrosion within the cooler, replaceable anodes are
installed at both the saltwater inlet and outlet
manifolds. These anodes are periodically inspected and
replaced according to the applicable maintenance
requirement card (MRC). A fluid temperature indicator
is located on the engine control panel.
AUXILIARY AIR FLASKS
The auxiliary air flask provides a means of storing
ship's air at 3,000 psi. In the event of a ship's air system
failure, the air stored in the auxiliary air flask can be
used to recharge the arresting engine.
The air flask is a cylindrical container with
hemispherical ends. One end of the air flask is provided
with a pipe tap for connecting an air line, which is used
for charging and venting. A drainage vent is located on
the underside of the air flask to drain condensate water.
Air can be supplied to the air unit of the arresting
engine from the auxiliary air flask by use of the
charging valve mounted on the main control panel.
3-16
FROM
AIR
EXPANSION
FLASK
FUSED
SWITCH
BOX
TO
VENT
FROM
HIGH-PRESSURE
AIR SUPPLY
CABLE ANCHOR
DAMPER
LIGHT BOX
FROM
AUXILIARY
AIR
SUPPLY
ABEf0314
Figure 3-14.Engine control panel.
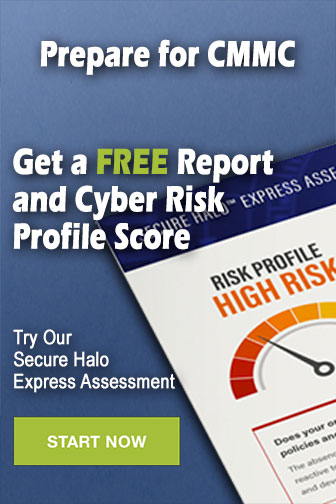