applicable technical manuals. Typical maintenance
includes the following:
LUBRICATION. As stated previously, proper lu-
brication is a MUST. But do not over-grease. After
lubrication, a small amount of grease may escape
from the grease reliefs under the head. This is normal.
But, if grease continues to escape the grease relief
fitting should be removed and inspected for damage,
or the bearing removed and its grease shield inspected
for damage. If grease escapes from around the pump
shaft, the bearing cover should be removed and the lip
on the shaft seal inspected for nicks, cuts, or distor-
tion. Replace if necessary.
MECHANICAL SEALS. No maintenance re-
quired. Replace if leakage occurs.
HEAD O-RINGS. If leakage occurs between the
head and the cylinder, the head should be removed
and both machined faces inspected for burrs, a cut or
damaged O-ring, or other imperfections. If the O-ring
is damaged in ANY way, replace it.
VANES. If the vanes are excessively worn, swol-
len, or jamming in the rotor slots, replace them.
PRESSURE CONTROL VALVE ADJUST-
MENT. Line up the suction side of the pump to a
storage tank, opening the required valves. Make sure
the pump discharge valve is closed. Start the pump,
remove the protective cap, and loosen the locknut.
Turn the adjustment screw until the desired pressure
is indicated on the discharge pressure gage. Tighten
the locknut, replace the protective cap, stop the pump,
and secure the suction side piping.
TROUBLESHOOTING. Table 4-3 lists typi-
cal malfunctions, probable causes, and corrective ac-
tion for rotary vane pumps.
PUMP COUPLINGS
All aviation fuel pumps are equipped with a type
of flexible coupling. This coupling allows connection
of the pump and motor (or gear reducer) shafts with a
minute amount of misalignment. The flexibility of the
Table 4-3.Rotary Vane Pump Troubleshooting Guide
4-16
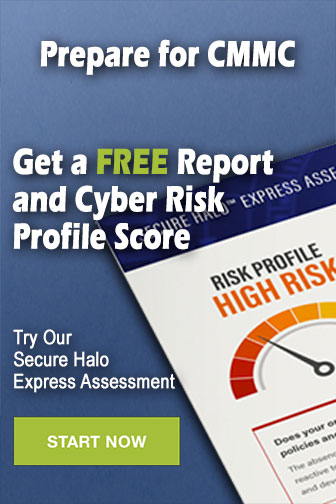