Material Delivery Unit (MDU)
The MDU is responsible for the delivery of material
to the customer within the established time frame. This
unit is also responsible for picking up material from the
customers and forwarding them to supply or
maintenance.
Material delivery unit is responsible for performing
the following tasks:
l
l
l
l
l
l
l
l
Receives material and associated documents
from the designated pick-up points.
Delivers material and associated documents to
the designated delivery points.
For repairable item issues, picks up the turn-in,
logs and records (if applicable) except when
delay turn-in is authorized. Validate the
CAGE/PN on the turn-in MAF against the issue
document. Sign and provide a copy of DD Form
1348 to the customer for use as proof of
repairable turn-in.
Deliver the turn-in to the
Aeronautical Material Screening Unit (AMSU)
via SSU.
Has the customer sign and annotate the date and
time on the issue document when material was
delivered.
Submits signed proof of delivery (POD) copy to
the unit assigned to process the applicable
documents.
Forwards warehouse refusal requisitions to the
RCU for further processing.
Receives EXREP or work stoppage notice from
DCU and picks up the applicable components
from the customers.
Delivers EXREP or work stoppage component
and associated documents to AMSU via SSU.
The NALCOMIS conversation codes primarily
used by MDU are N613, N615, N618, N628, and N630.
The supporting conversation codes used by MDU are
N606, N624, N635, N652, N655, N658, N668, N676,
and N693. These conversation codes are described in
NALCOMIS users manual.
Pre-Expended Bin (PEB) Unit
The PEB unit is responsible for managing
consumable items that are authorized to be
pre-expended. Pre-xpended means the item has been
paid for by an appropriate account. Since the items are
pre-paid, material issued to supported maintenance
activities will not require another financial transaction.
The PEBs are located in areas that are readily accessible
to maintenance personnel. When feasible, PEBs should
be located where they can be observed by PEB
personnel to ensure their proper usage.
To be included in the PEB, the item must have a
minimum demand frequency of three per month. The
supply officer and the aviation maintenance officer are
jointly responsible for determining the items to be
added to or purged from the PEB. The total quantity of
each item must not exceed an estimated 30-day supply.
The PEB stock level requirements for the Metrology
and Calibration Program are determined from usage
data collected from metrology equipment recall cards
by ASD. Items with a unit cost of 0.00 or less can
be routinely included in the PEB. Eligible items with a
unit cost over 0.00 will be authorized by the
commanding officer.
The SRS is responsible for replenishing stock in
PEB. The stock records are reviewed quarterly to
ensure the items meet the demand frequency
requirements. The items that do not have sufficient
usage are purged and returned to the supporting supply
department. As a minimum, any item that does not have
a demand within the last 12 months is purged from the
PEB.
Pilferable PEB items are retained within an
enclosure with access limited to authorized personnel
only. Various items are NOT authorized for inclusion
in the PEB. These items are listed in volume 1, chapter
19, of OPNAVINST 4790.2.
The NALCOMIS conversation code N603 is used
to initiate a requisition for replenishment of material for
the PEB. This conversation code contains an option to
produce the PEB requisition listing. Refer to the
NALCOMIS users manual for detailed information
about conversation code N603.
Component Control Section (CCS)
The CCS performs repairable management
functions in support of the Navy supply system. The
CCS is responsible for accounting for repairable in
storage, repair cycle, and holding areas within the
organization. The CCS consists of four units. hey are
the Document Control Unit (DCU), Local Repair Cycle
Asset (LRCA) Storage Unit, Supply Screening Unit
(SSU), and Awaiting Parts (AWP) Unit. The CCS is the
direct link between the supply department and the
intermediate maintenance activity (IMA).
7-12
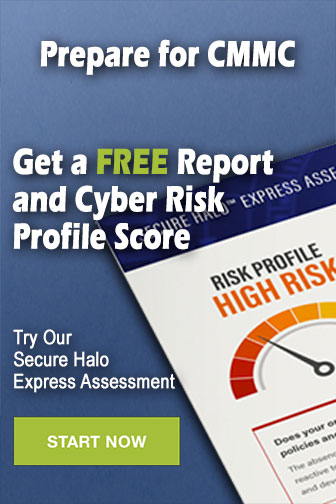